Table of contents
Drawn cup roller clutches
- Product design
- Load carrying capacity
- Compensation of angular misalignments
- Lubrication
- Sealing
- Speeds
- Noise
- Temperature range
- Cages
- Internal clearance
- Dimensions, tolerances
- Suffixes
- Structure of product designation
- Dimensioning
- Design of the adjacent construction
- Mounting and dismounting
- Legal notice regarding data freshness
Drawn cup roller clutches
Drawn cup roller clutches:
- are one-way clutches, which transmit torques in one direction ➤ Figure
- are available with or without an integrated bearing arrangement ➤ Figure, ➤ Figure and ➤ Figure
- give very precise indexing
- allow high indexing frequencies
- have a low overrunning frictional torque
- are available with or without greasing
- are particularly compact in a radial direction and therefore permit extremely compact designs
- are suitable for housing materials made from steel, light metal or plastic
- can be combined with drawn cup needle roller bearings with open ends HK and drawn cup needle roller bearings with closed end BK
- have an extensive range of applications, for example as indexing clutches, back-stopping clutches and overrunning clutches ➤ Figure
Drawn cup roller clutches in tandem arrangement in an indexing system
|
![]() |
Product design
Design variants
Drawn cup roller clutches are available:
- without bearing arrangement ➤ Figure
- with bearing arrangement (rolling or plain bearing) ➤ Figure and ➤ Figure
Drawn cup roller clutches
Drawn cup roller clutches are one-way clutches
These drawn cup roller clutches comprise thin-walled, drawn outer rings with a series of ramps on the inside diameter, plastic cages and needle rollers, which serve as clamping elements. Steel or plastic springs hold the needle rollers in their clamped position. Drawn cup roller clutches can transmit high torques in one direction and are particularly compact in a radial direction. The roller clutches are available with and without support bearing arrangements.
Suitable for applications with high indexing frequencies
Drawn cup roller clutches give very precise indexing, since the individual spring loading of the needle rollers ensures continuous contact between the shaft, needle rollers and ramps. They allow high indexing frequencies due to their low mass and the resulting low moment of inertia of the clamping elements. They also have a low overrunning frictional torque.
Preferred areas of application
Drawn cup roller clutches can be used in various applications such as indexing clutches, back-stopping clutches and overrunning clutches. In these cases, the drawn cup roller clutch performs an overrunning or locking function.
Drawn cup roller clutches should not be used if a malfunction could lead to personal injury. New applications, especially those involving extreme conditions, should first be verified by tests. Correct functioning can only be guaranteed if the concentricity error between the support bearing and the shaft can be kept to a low value.
Drawn cup roller clutches without bearing arrangement
Suitable for supporting torques only
Roller clutches HF do not have a bearing arrangement, i. e. they transmit torques only and, as a result, are unable to support any radial forces ➤ Figure. In the case of these roller clutches, concentricity to the shaft axis must be secured by additional rolling bearings or drawn cup roller clutches with a bearing arrangement must be used. The drawn cup roller clutches are available with and without knurling.
Drawn cup roller clutches without knurling
Drawn cup roller clutches without knurling are available with steel or plastic pressure springs ➤ Figure. Bearings with plastic springs have the suffix KF ➤ section.
Drawn cup roller clutches with knurling
For improved torque transmission in plastic housings, drawn cup roller clutches are available with a knurled outside surface. These drawn cup roller clutches have the suffix R ➤ section. The knurling can be applied to part of the drawn cup or over its entire length. The drawn cup roller clutches are also available with steel or plastic pressure springs. Roller clutches with plastic springs have the suffix KF ➤ section.
Drawn cup roller clutches without bearing arrangement, with and without knurling
|
![]() |
Drawn cup roller clutches with bearing arrangement
Also suitable for supporting radial forces
Due to the integrated plain or rolling bearing, roller clutches HFL can also support radial forces in addition to torques ➤ Figure and ➤ Figure. The drawn cup roller clutches are available with and without knurling.
Drawn cup roller clutches without knurling
Drawn cup roller clutches without knurling are available with steel or plastic pressure springs ➤ Figure and ➤ Figure. Drawn cup roller clutches with plastic springs have the suffix KF ➤ section.
Drawn cup roller clutches with knurling
For improved torque transmission in plastic housings, drawn cup roller clutches are available with a knurled outside surface. These drawn cup roller clutches have the suffix R ➤ section. The knurling can be applied to part of the drawn cup or over its entire length. These drawn cup roller clutches are also available with steel or plastic pressure springs. Roller clutches with plastic springs have the suffix KF ➤ section.
Drawn cup roller clutches with plain bearing arrangement, with and without knurling Fr = radial load
|
![]() |
Drawn cup roller clutch with rolling bearing arrangement, without knurling Fr = radial load
|
![]() |
Clamping direction of the drawn cup roller clutch
An arrow on the end face of the drawn cup indicates the clamping direction of the drawn cup roller clutch. The roller clutch clamps when the drawn cup is rotated in the direction of the arrow.
Load carrying capacity
Roller clutches with a support bearing arrangement accommodate radial forces
Depending on the design (with or without bearing arrangement), drawn cup roller clutches can either transmit torques only or additional radial loads ➤ section, ➤ Figure and ➤ Figure. For roller clutches without bearing arrangement, radial forces must be supported by additional bearings.
Transmissible torque
The rigidity of the housing determines the transmissible torque
Transmission of torque requires a rigid housing. The transmissible torque is therefore dependent on the shaft and housing material, the shaft hardness, the wall thickness of the housing and the shaft and housing tolerances. When calculating the torque, the maximum drive torque and the moment of inertia of the masses during acceleration must be taken into consideration.
Limiting load
Do not exceed the limiting load
In the case of drawn cup roller clutches with plain bearings, the product calculated from the actual speed n and radial load FR must not exceed the value stated for the limiting load (Fr · n)max. The operating limits are determined by the limiting speeds stated in the product tables and the permissible radial load.
Indexing accuracy and indexing frequency
The roller clutch must not be overloaded
In order not to overload the clutch, the inertia of the entire system must be taken into consideration. The high indexing accuracy is due to the individual spring loading of the needle rollers, which ensures continuous contact between the shaft, needle rollers and clamping surface. The indexing accuracy is influenced by the indexing frequency, lubrication, fitting tolerances, adjacent construction, elastic deformation of the adjacent parts and the drive method, either through the shaft or the housing. Optimum accuracy is achieved if the drive is via the shaft.
High indexing frequencies due to low mass
High indexing frequencies are due to the low mass and the resulting low moment of inertia of the clamping elements.
Frictional torque and frictional energy
For pattern of frictional torque ➤ Figure. The frictional energy at idle is dependent on whether the shaft or the outer ring is rotating ➤ Figure.
Frictional torque during idling, as a function of shaft diameter MR = frictional torque during idling d = shaft diameter |
![]() |
Frictional energy during idling, as a function of speed NR = frictional energy during idling n = speed nGA = limiting speed with rotating outer ring nGW = limiting speed with rotating shaft |
![]() |
Rotating outer ring
Due to the centrifugal force, the needle rollers may lift off the shaft
If the outer ring rotates, the frictional energy increases with speed at first but then, due to the centrifugal force of the needle rollers, it decreases gradually towards zero. At this speed, there is no longer any frictional contact between the needle rollers and the shaft. Due to the increasing centrifugal force, the needle rollers lift off the shaft.
Compensation of angular misalignments
Concentricity is an essential precondition for correct functioning of the roller clutch. Correct functioning can only be guaranteed if the concentricity error between the support bearing and the shaft can be kept to a low value.
Lubrication
A grease to GA26 is used for initial greasing
The roller clutches are greased using a lithium soap grease to GA26. In many cases, the initial greasing is sufficient to last the operating life of the bearings. For applications with oil lubrication, roller clutches are available without greasing. These roller clutches are coated with a preservative. For general applications (mixed operation involving locking and overrunning), the Schaeffler initial greasing has proved effective. In order to ensure optimum function, it may be necessary to use different lubricants. The suitability of the lubricant must then be verified by means of tests.
For applications in which one operating condition (overrunning or locking) is heavily predominant, a special greasing should be used. In this case, please consult Schaeffler.
A grease operating life cannot be calculated
It is not possible to calculate the grease operating life or lubrication interval for drawn cup roller clutches. If relubrication is carried out, oil should used for lubrication or a changeover to oil lubrication should generally be made. At temperatures < –10 °C and speeds > 0,7 nG, recommendations on lubrication should be requested. At temperatures over +70 °C, oil lubrication should be used. The oil level should be such that, when the drawn cup roller clutch is stationary and the axis is horizontal, it is immersed approx. 1/3 in the oil bath.
Suitable lubricating oils
Suitable oils are CL and CLP to DIN 51517 or HL and HLP to DIN 51524. Viscosity classes ➤ Table.
Compatibility with plastic cages
When using bearings with plastic cages, compatibility between the lubricant and the cage material must be ensured if synthetic oils, lubricating greases with a synthetic oil base or lubricants containing a high proportion of EP additives are used.
Viscosity classes
Operating temperature |
Viscosity class |
|
---|---|---|
°C |
||
from |
to |
|
+15 |
+30 |
ISO VG 10 |
+15 |
+90 |
ISO VG 32 |
+60 |
+120 |
ISO VG 100 |
Sealing
Drawn cup roller clutches (with and without bearing arrangement) are supplied without seals. Contaminants (dust, dirt and moisture) can impair the function and operating life of roller clutches.
Sealing of the bearing position with sealing rings G or SD
Effective sealing elements for use in sealing open drawn cup roller clutches with a risk of contamination
If there is a risk of contamination, sealing rings of economical series G or SD should be fitted ➤ link. The sealing rings are designed as contact seals and are arranged in front of the roller clutch. They protect the bearing position reliably against contamination, spray water and excessive loss of grease. The sealing rings are matched to the small radial dimensions of the drawn cup roller clutches and can be combined with wider inner rings of series IR. They are very easy to fit, since they are simply pressed into the housing bore.
Speeds
Speeds for rotating shaft or rotating outer ring
The limiting speeds nGW and nGA in the product tables are valid for oil and grease lubrication. The limiting speed nGW is valid for a rotating shaft, while nGA is valid for a rotating outer ring.
Noise
Schaeffler Noise Index
The Schaeffler Noise Index (SGI) is not yet available for this bearing type ➤ link. The data for these bearing series will be introduced and updated in stages.
Temperature range
Possible operating temperatures of drawn cup roller clutches ➤ Table.
Permissible temperature ranges
Operating temperature |
Drawn cup roller clutches |
---|---|
|
–10 °C to +70 °C, limited by the lubricant |
In the event of anticipated temperatures which lie outside the stated values, please contact Schaeffler.
Cages
Plastic cages are used in the guidance of rolling elements for roller clutches and for integrated support bearing arrangements supported by rolling elements.
Internal clearance
The enveloping circle diameter Fw applies instead of the radial internal clearance
In the case of bearings without inner ring, the enveloping circle dimension Fw is used instead of the radial internal clearance. The enveloping circle is the inner inscribed circle of the needle rollers in clearance-free contact with the outer raceway. In drawn cup roller clutches with a rolling bearing arrangement, the enveloping circle diameter Fw of the bearings once fitted (in the solid section ring gauge) is approximately in tolerance class F8. Upper and lower deviations of enveloping circle diameter for tolerance class F8 ➤ Table.
Deviations of enveloping circle diameter for drawn cup roller clutches supported by rolling bearings
Enveloping circle diameter Fw |
Tolerance class F8 |
||
---|---|---|---|
mm |
Tolerance for enveloping circle diameter Fw |
||
upper deviation |
lower deviation |
||
over |
up to |
μm |
μm |
3 |
6 |
+28 |
+10 |
6 |
10 |
+35 |
+13 |
10 |
18 |
+43 |
+16 |
18 |
30 |
+53 |
+20 |
30 |
50 |
+64 |
+25 |
Dimensions, tolerances
Deviations and tolerances of drawn cup roller clutches are not standardised. The thin-walled outer cups adopt the dimensional and geometrical accuracy of the housing bore.
Suffixes
For a description of the suffixes used in this chapter ➤ Table and medias interchange http://www.schaeffler.de/std/1B69.
Suffixes and corresponding descriptions
Suffix |
Description of suffix |
|
---|---|---|
‒ |
Steel springs |
Standard |
KF |
Plastic pressure springs |
Standard |
R |
Knurled outside surface |
Standard |
RR |
Drawn cup roller clutch with Corrotect coating |
Special design, available by agreement |
Structure of product designation
Examples of composition of product designation
The designation of drawn cup roller clutches follows a set model. Examples ➤ Figure and ➤ Figure.
Drawn cup roller clutch without bearing arrangement, without knurling: designation structure |
![]() |
Drawn cup roller clutch with bearing arrangement, plastic pressure springs, with knurling: designation structure |
![]() |
Dimensioning
The size is determined on the basis of the load carrying capacity of the drawn cup roller clutch relative to the loads and the requirements for rating life and operational reliability ➤ section.
Design of the adjacent construction
Design of housing bore
Support outer cup over entire circumference and width
Suitable housing materials are steel, light metal or plastic. In order to allow full utilisation of the performance capability of drawn cup roller clutches and thus also achieve the requisite rating life, sufficient rigid support must be provided for the outer cups in the housing. The support for the outer cup in the housing bore can be produced as a cylindrical seating surface. The seating surfaces for the outer cup and the raceway for the rolling elements or inner ring (if the bearing arrangement is not produced as a direct bearing arrangement) should not be interrupted by grooves, holes or other recesses. The accuracy of the mating parts must meet specific requirements, the bore tolerances for the housing bore (recommended tolerance classes) are dependent on the housing material ➤ Table and ➤ Table. The surface quality of the housing bore should be Ramax 0,8. The cylindricity tolerance of the housing bore in metal housings should be within the tolerance grade IT5/2.
Due to the thin-walled outside surface, the roller clutches only adopt their precise geometry once they have a tight fit. As a result, the accuracy of the locating bore essentially determines the geometrical accuracy of the drawn cup and thus the functioning of the clutch.
Provide lead chamfer on the housing bore
For the drawn cup roller clutches to be mounted without damage, the housing bore must have a lead chamfer of 15°.
Design of housing bore
Series |
Springs |
Bore |
|||
---|---|---|---|---|---|
Housing material |
|||||
Steel, cast iron |
Light metal |
Max. bore |
|||
HF, HFL |
Steel |
N6 Ⓔ (N7 Ⓔ)1) |
R6 Ⓔ (R7 Ⓔ)1) |
‒ |
|
HF..-KF, HFL..-KF |
Plastic |
N7 Ⓔ |
R7 Ⓔ |
‒ |
|
HF..-R, HFL..-R |
Steel |
‒ |
‒ |
D |
0 |
HF..-KF-R, HFL..-KF-R |
Plastic |
‒ |
‒ |
D |
0 |
HFL0606-KF-R, HFL0806-KF-R |
Plastic |
‒ |
‒ |
D |
0 |
- The values in brackets can be used if the actual torque is no more than 50% of the permissible torque Md per in accordance with the product table.
- Guide values as a function of the plastic used. Outside diameter D ➤ link.
Minimum wall thickness for metal housings
Maximum transmissible torque
For metal housings, the maximum transmissible torque Md per max is determined as a function of the diameter ratio QA to ➤ Figure (steel housing) or to ➤ Figure (aluminium housing), see calculation examples.
Guide values for QA max with steel and aluminium as housing materials ➤ Table.
Guide values
Housing material |
Diameter ratio QA max |
---|---|
Steel |
0,8 |
Aluminium |
0,6 |
The comparative stress σv must not exceed the yield stress of the housing material.
Steel housing
Calculation example
For drawn cup roller clutches HF0612, the maximum transmissible torque Md per max should be determined ➤ Figure:
Drawn cup roller clutch | HF0612 |
Housing | Steel |
Housing bore tolerance | N6 Ⓔ |
Permissible housing stress (Rp0,2) σv | 450 N/mm2 |
Diameter ratio QA of housing | 0,9 |
Permissible torque Md per | in accordance with product table |
Calculation
Md per max | |
= 60% Md per | |
= 0,6 * 1, 76 Nm | |
= 1,056 Nm |
Steel housing Modulus of elasticity E = 210 000 N/mm2 QA = diameter ratio of housing DAi = housing bore DAa = housing outside diameter Md per = permissible torque Md per max = maximum transmissible torque σv = comparative stress |
![]() |
Aluminium housing
Calculation example
For drawn cup roller clutch HF1616, the diameter ratio QA of the housing should be determined ➤ Figure:
Drawn cup roller clutch | HF1616 |
Housing | Aluminium |
Housing bore tolerance | R6 Ⓔ |
Permissible housing stress (Rp0,2) σv | 250 N/mm2 |
Maximum transmissible torque Md per max | 10 Nm |
Permissible torque Md per | in accordance with product table |
giving Md per max /Md per | 50% |
Calculation
QA | = DAi /DAa ≤ 0,7 |
DAa | ≧ DAi /0,7 = 22 mm/0,7 |
= 31,5 mm |
Aluminium housing Modulus of elasticity QA = diameter ratio of housing DAi = housing bore DAa = housing outside diameter Md per = permissible torque Md per max = maximum transmissible torque σv = comparative stress |
![]() |
Minimum wall thickness for plastic housing
For plastic housings, drawn cup roller clutches with a partially or fully knurled outside surface should be used (suffix R).
The guide value for the minimum wall thickness of plastic housings is:
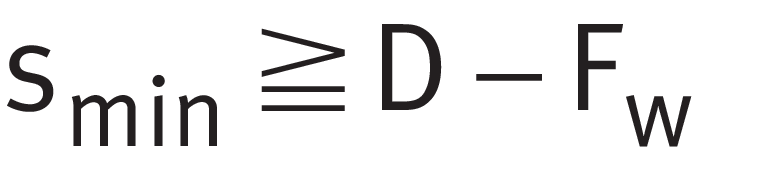
Legend
smin | mm |
Minimum wall thickness |
D | mm |
Outside diameter of roller clutch |
Fw | mm |
Enveloping circle |
Axial location
A tight fit is usually sufficient for axial location
Drawn cup roller clutches give very easy mounting and permit simple adjacent constructions. The drawn cup roller clutches are pressed into the housing bore and require no further axial location.
The precondition for this is, however, that the specifications in accordance with ➤ Table are observed.
Design of the shaft/raceway
Producing the raceway as a rolling bearing raceway
Drawn cup roller clutches HF/HFL are usually used without an inner ring. In order to guarantee correct functioning of the drawn cup roller clutches, the raceway for the rolling elements on the shaft must be produced as a rolling bearing raceway (hardened and ground). The surface hardness of the raceways mus be 670 HV to 840 HV, the case hardening depth CHD must be sufficiently large (CHD ≧ 0,3 mm). Design of raceways ➤ Table. If the shaft cannot be produced as a raceway, the bearings can be combined with inner rings IRor LR.
Provide lead chamfer on the housing bore
For the bearings to be mounted without damage, the shaft must have a lead chamfer of 10° to 15° with a width of approx. 1 mm.
Design of shaft
Series |
Springs |
Shaft |
|||
---|---|---|---|---|---|
Tolerance class1) |
Roundness tolerance |
Parallelism tolerance |
Recommended mean roughness value |
||
Ramax (Rzmax) |
|||||
max. |
max. |
μm |
|||
HF, HFL |
Steel |
h5 (h6)2) |
IT3 |
IT3 |
0,4 (2) |
HF..-KF, HFL..-KF |
Plastic |
h8 |
|||
HF..-R, HFL..-R |
Steel |
h5 (h6)2) |
|||
HF..-KF-R, HFL..-KF-R |
Plastic |
h8 |
|||
HFL060t6-KF-R, HFL0806-KF-R |
Plastic |
h9 |
- The envelope requirement Ⓔ applies.
- The values in brackets can be used if the actual torque is no more than 50% of the permissible torque Md per.
Mounting and dismounting
Protect drawn cup roller clutches against dust, dirt and moisture; contaminants can impair the function and operating life of roller clutches. Pressing-in forces must never be directed through the rolling elements. Drawn cup roller clutches must not be tilted during pressing-in, as this may damage the needle rollers and raceways.
Retention for transport
Drawn cup roller clutches are normally packed individually in the case of small quantities. Where larger quantities are involved, drawn cup roller clutches are placed in a specific orientation in blister packaging and delivered in this form. The blister packaging then serves to retain the parts in position during transport.
Removing the drawn cup roller clutches from the packaging
Drawn cup roller clutches should only be removed from their original packaging immediately before assembly. If roller clutches are removed from a batch packaged with dry preservative, the package must be closed again immediately. The protective vapour phase can be maintained only in the closed package. Ungreased drawn cup roller clutches are coated with a preservative. Lubrication with oil must take place after pressing-in, in accordance with the specifications.
Storage
Drawn cup roller clutches should be stored:
- in dry, clean rooms with the room temperature as constant as possible
- at a relative humidity of max. 65%
Storage period
The storage period for greased drawn cup roller clutches is limited by the shelf life of the lubricating grease.
Mounting using a fitting mandrel
Drawn cup roller clutches should only be pressed into the locating bore using a special fitting mandrel. Attention must be paid to the clamping direction of the roller clutch. The clamping direction is indicated by an arrow on the end face of the drawn cup.
The drawn cup roller clutch clamps if it is rotated in the direction of the arrow.
Functional inspection
Clutches without knurling
The function of these roller clutches is checked in a housing with the minimum wall thickness determined according to ➤ Figure or thicker. The housing bore and shaft tolerances must be observed ➤ Table and ➤ Table.
Clutches with knurling
The function of these clutches is checked before they are pressed in. In this case, the inspection criteria are the clamping effect and idling.
For any questions relating to the mounting of drawn cup roller clutches, please consult Schaeffler.
Schaeffler Mounting Handbook
Drawn cup roller clutches must be handled with great care
In order that drawn cup roller clutches can function correctly and achieve the envisaged operating life without detrimental effect, they must be handled with care.
The Schaeffler Mounting Handbook MH 1 gives comprehensive information about the correct storage, mounting, dismounting and maintenance of rotary rolling bearings http://www.schaeffler.de/std/1B68. It also provides information which should be observed by the designer, in relation to the mounting, dismounting and maintenance of bearings, in the original design of the bearing position. This book is available from Schaeffler on request.
Legal notice regarding data freshness
The further development of products may also result in technical changes to catalogue products
Of central interest to Schaeffler is the further development and optimisation of its products and the satisfaction of its customers. In order that you, as the customer, can keep yourself optimally informed about the progress that is being made here and with regard to the current technical status of the products, we publish any product changes which differ from the printed version in our electronic product catalogue.
We therefore reserve the right to make changes to the data and illustrations in this catalogue. This catalogue reflects the status at the time of printing. More recent publications released by us (as printed or digital media) will automatically precede this catalogue if they involve the same subject. Therefore, please always use our electronic product catalogue to check whether more up-to-date information or modification notices exist for your desired product.