Table of contents
Axial needle roller bearings
- Bearing design
- Load carrying capacity
- Compensation of angular misalignments
- Lubrication
- Sealing
- Speeds
- Noise
- Temperature range
- Cages
- Internal clearance
- Dimensions, tolerances
- Suffixes
- Structure of bearing designation
- Dimensioning
- Minimum load
- Design of bearing arrangements
- Mounting and dismounting
- Legal notice regarding data freshness
- Further information
Axial needle roller bearings
Axial needle roller bearings are particularly suitable where:
- high axial forces occur in one direction but no radial loads are present (the bearings may only be subjected to axial load ➤ section)
- the load carrying capacity of comparable axial deep groove ball bearings is no longer adequate and the very high axial load carrying capacity of axial cylindrical roller bearings is not yet necessary ➤ Figure
- higher speeds occur in addition to high axial loads
- the bearing arrangement must have very high axial rigidity
- the axial space available is extremely small ➤ Figure
- the bearing parts can or must be mounted separately
- the bearing arrangement is not configured but, for cost reasons, ready‑to-fit standard bearings are to be used.
Axial needle roller bearing and axial deep groove ball bearing – comparison of load carrying capacity and design envelope Fa = axial load Ca = basic dynamic load rating Dw = diameter of needle roller T = axial section height of axial deep groove ball bearing |
![]() |
Bearing design
Design variants
Axial needle roller bearings are available as:
- complete axial needle roller bearings (comprising a needle roller and cage assembly and axial bearing washers) ➤ Figure
- bearings with centring spigot (prefix AXW) ➤ Figure and ➤ Figure.
Furthermore, Schaeffler supplies axial needle roller bearings by agreement for specific applications, for example with tabs to prevent rotation. Such bearings are used, due to their low axial section height, in applications such as automotive manual gearshift transmissions.
Axial needle roller bearings
Ready-to-fit bearing units with very small axial space
Axial needle roller bearings are part of the group of axial roller bearings. In contrast to the ball, the roller has a larger contact area perpendicular to the roller axis. As a result, it can transmit higher forces, has greater rigidity and allows smaller rolling element diameters under the same load. The single row, ready-to-fit bearings comprise flat, ribless axial bearing washers between which axial needle roller and cage assemblies are arranged ➤ Figure. Their axial section height corresponds only to the diameter of the needle rollers plus the thickness of the washers. Due to this design, the bearings are extremely small in axial height ➤ dimension table. The rolling elements are retained and guided by axial cages. The needle rollers are made from through-hardened rolling bearing steel 100Cr6. They have a hardness of at least 670 HV and profiled ends, i. e. they have a slight lateral curvature towards the ends. The modified line contact between the needle rollers and raceways prevents damaging edge pressures. This in turn has a positive effect on the operating life of the bearings.
Due to the extensive possible combinations, the bearing parts for axial needle roller bearings are always supplied individually, i. e. the corresponding axial needle roller and cage assemblies and axial bearing washers in the product tables must always be ordered together ➤ Figure, ➤ Figure, ➤ section and ➤ dimension table.
Axial needle roller bearing Fa = axial load
|
![]() |
Axial needle roller and cage assemblies
The axial section height corresponds to the needle roller diameter
Axial needle roller and cage assemblies AXK comprise geometrically stable plastic or metal cages fitted with a large number of needle rollers ➤ Figure. Due to the high uniformity of diameter (the needle rollers are sorted to very small diameter tolerances) of the needle rollers with each other, this gives very uniform loading of the rolling elements ➤ Table. Since the axial section height of the cage assemblies is determined purely by the needle roller diameter, the bearings require only an extremely small axial design space.
Suitable as a direct bearing arrangement or in conjunction with axial bearing washers
The axial needle roller and cage assemblies are generally combined with axial bearing washers ➤ Figure and ➤ Figure. If they are to be used directly – i. e. without these washers – in the adjacent construction, the raceway for the needle rollers must be produced as a rolling bearing raceway ➤ section.
Axial bearing washers
Suitable as shaft or housing locating washers
Axial bearing washers AS are suitable for axial needle roller and cage assemblies AXK. They are punched, through hardened, polished and suitable for use as shaft or housing locating washers. Housing locating washers are externally centred, shaft locating washers are internally centred ➤ Figure and ➤ section. They are used if the adjacent machine parts cannot be used as a raceway for the rolling elements but are sufficiently rigid and geometrically precise.
The use of complete axial needle roller bearings (axial cylindrical roller and cage assembly AXK with axial bearing washers AS) is only appropriate, for example, if high speeds occur and the bearing washers must therefore be precisely centred or the contact surfaces for the rolling elements cannot be configured as a rolling bearing raceway.
Axial bearing washers
|
![]() |
Axial bearings with centring spigot
The centring spigot gives simplified mounting of the bearings
Axial needle roller bearings AXW comprise a housing locating washer with a centring spigot into which an axial needle roller and cage assembly AXK is inserted. With the aid of the centring spigot, the housing locating washer can be precisely centred in the housing bore. This gives easier mounting of the bearings. The running surface for the needle roller and cage assembly must be produced as a rolling bearing raceway, i. e. it must be hardened and ground.
Suitable for the support of axial loads only
Axial bearings with a centring spigot can only support axial loads in one direction. In order to support combined radial/axial loads, however, these bearings can be combined with the following radial needle roller bearings:
- drawn cup needle roller bearings with open ends and with closed end (direct bearing arrangement) ➤ Figure
- needle roller bearings with or without inner ring ➤ Figure
Such combinations give very compact and economical bearing arrangements.
Needle roller axial bearings with centring spigot, combined with drawn cup needle roller bearings with open ends Fa = axial load Fr = radial load
|
![]() |
Needle roller axial bearings with centring spigot, combined with needle roller bearings Fa = axial load Fr = radial load
|
![]() |
Load carrying capacity
For high axial loads acting in one direction
Single row axial needle roller bearings can support high axial loads as well as axial shock loads in one direction, but must not be subjected to radial load ➤ section. Radial loads must be supported by means of an additional bearing ➤ Figure and ➤ Figure.
Compensation of angular misalignments
The bearings do not permit any skewing between the shaft and housing. If angular misalignments occur between the locating surfaces on the shaft and in the housing, this will cause damage to the bearing and a reduction in its operating life.
Lubrication
Oil or grease lubrication is possible
Axial needle roller bearings and axial needle roller and cage assemblies are not greased. The bearings must be lubricated with oil or grease.
Compatibility with plastic cages
When using bearings with plastic cages, compatibility between the lubricant and the cage material must be ensured if synthetic oils, lubricating greases with a synthetic oil base or lubricants containing a high proportion of EP additives are used.
If there is any uncertainty regarding the suitability of the selected lubricant for the application, please consult Schaeffler or the lubricant manufacturer.
Observe oil change intervals
Aged oil and additives in the oil can impair the operating life of plastics at high temperatures. As a result, stipulated oil change intervals must be strictly observed.
Sealing
Provide seals in the adjacent construction
The bearings are not sealed; i. e. sealing of the bearing position must be carried out in the adjacent construction. This must reliably prevent:
- moisture and contaminants from entering the bearing
- the egress of lubricant from the bearing position
Speeds
Limiting speeds and reference speeds in the product tables
The product tables give two speeds for the bearings ➤ dimension table:
- the kinematic limiting speed nG
- the thermal speed rating nϑr
Limiting speed
The limiting speed nG is the kinematically permissible speed of a bearing. Even under favourable mounting and operating conditions, this value should not be exceeded without prior consultation with Schaeffler ➤ link. The values in the product tables are valid for oil lubrication.
Values for grease lubrication
For grease lubrication, 25% of the value stated in the product tables is permissible in each case.
Reference speeds
nϑr is used to calculate nϑ
The thermal speed rating nϑr is not an application-oriented speed limit, but is a calculated ancillary value for determining the thermally safe operating speed nϑ ➤ link.
Noise
Schaeffler Noise Index
The Schaeffler Noise Index (SGI) is not yet available for this bearing type ➤ link. The data for these bearing series will be introduced and updated in stages.
Temperature range
Limiting values
The operating temperature of the bearings is limited by:
- the dimensional stability of the bearing washers and needle rollers
- the cage
- the lubricant.
Possible operating temperatures for axial needle roller bearings ➤ Table.
Permissible temperature ranges
Operating temperature |
Corrosion-resistant design |
Bearings with sheet steel cage |
---|---|---|
|
–20 °C to +120 °C |
–20 °C to +120 °C |
In the event of anticipated temperatures which lie outside the stated values, please contact Schaeffler.
Cages
The standard cages are made from sheet steel
Standard cages ➤ Table. Other cage designs are available by agreement. With such cages, however, suitability for high speeds and temperatures as well as the basic load ratings may differ from the values for the bearings with standard cages.
For high continuous temperatures and applications with difficult operating conditions, bearings with sheet metal cages should be used. If there is any uncertainty regarding cage suitability, please consult Schaeffler.
Cage, cage suffix, inner cage diameter
Bearing series |
Solid cage |
Sheet steel cage |
Corrosion-resistant design (with Corrotect coating) |
---|---|---|---|
TV |
RR |
||
Inner cage diameter |
|||
AXK |
up to 8 |
from 10 |
Available by agreement |
AXW |
– |
from 10 |
Available by agreement |
Internal clearance
Axial clearance and preload are determined by the application
In the case of axial needle roller bearings, the internal clearance (axial clearance) is only achieved when the bearings are mounted. The requisite axial clearance of the bearing arrangement is dependent on the application and must take account of the conditions in the bearing arrangement while warm from operation and subjected to load. If axial needle roller bearings are subjected to vibrations while under predominantly static load, for example, they must be lightly preloaded. Preload can be applied, for example, using calibrated sheets (shims). Other suitable means include shaft nuts, disc springs etc. ➤ section. It must always be ensured that no slippage occurs in operation between the rolling elements and raceways ➤ section.
If there is any uncertainty regarding correct setting, please consult Schaeffler.
Dimensions, tolerances
The dimensions of special bearings (F../Z..) may deviate from the standard.
Dimension standards
The main dimensions of axial needle roller bearings correspond to ISO 104:2015. The main dimensions of axial needle roller and cage assemblies correspond to DIN 5405-2:2016, while those of axial bearing washers correspond to DIN 5405-3:2016. Axial needle roller bearings with centring spigot are not standardised.
Tolerances
Axial bearing washers adapt to the accuracy of the abutment surface. They are flat under a minimum concentric load of 200 N.
Tolerances for the bore and outside diameter as well as for the width of the bearing parts ➤ Table and ➤ Figure.
The sort tolerances and sort intervals of the needle roller diameters correspond to ISO 3096:1996 or DIN 5402-3:2012, grade G2.
The diameter sort tolerance of the needle rollers in the axial needle roller and cage assemblies AXW is 2 μm.
Tolerances of bearing parts
Series |
Bore |
Outside diameter |
Height |
|||
---|---|---|---|---|---|---|
Tolerance class |
Tolerance class |
Deviations |
||||
mm |
||||||
AXK |
Dc1 |
E11 |
Dc |
c12 |
Dw |
0 –0,01 |
AXW |
Dc1 |
E12 |
‒ |
‒ |
B |
0 –0,2 |
AS |
d |
E12 |
D |
e12 |
B1 |
±0,05 |
Bearing parts
|
![]() |
Suffixes
For a description of the suffixes used in this chapter ➤ Table and medias interchange http://www.schaeffler.de/std/1B69.
Suffixes and corresponding descriptions
Suffix |
Description of suffix |
|
---|---|---|
RR |
Corrosion-resistant design, |
Special design, |
TV |
Plastic cage made from |
Standard |
Structure of bearing designation
Examples of composition of bearing designation
The designation of bearings follows a set model. Examples ➤ Figure and ➤ Figure. The composition of designations for axial needle roller and cage assemblies and axial bearing washers is subject to DIN 623-1 ➤ Figure.
Axial needle roller bearing, comprising axial needle roller and cage assembly and axial bearing washers |
![]() |
Axial needle roller bearing with centring spigot, combined with axial bearing washer and drawn cup needle roller bearing with open ends |
![]() |
Dimensioning
Equivalent dynamic bearing load
Axial cylindrical roller bearings can only support axial forces ➤ section. In the rating life equation, P is therefore substituted by the value for Fa ➤ Equation.
Equivalent dynamic load
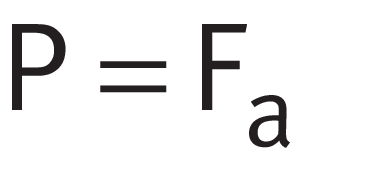
Legend
P | N |
Equivalent dynamic bearing load |
Fa | N |
Axial load. |
Equivalent static bearing load
Combined loads are not possible
In relation to the direction of load, the same conditions apply as for the equivalent dynamic bearing load, i. e. combined loads are not permissible. In the rating life equation, P0 is therefore substituted by the value for F0a ➤ Equation.
Equivalent static load
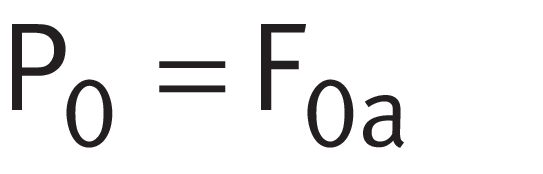
Legend
P0 | N |
Equivalent static bearing load |
F0a | N |
Largest axial load present (maximum load). |
Static load safety factor
S0 = C0/P0
In addition to the basic rating life L (L10h), it is also always necessary to check the static load safety factor S0 ➤ Equation.
Static load safety factor
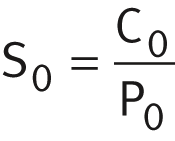
Legend
S0 |
Static load safety factor |
|
C0 | N |
Basic static load rating |
P0 | N |
Equivalent static bearing load. |
Minimum load
Rolling bearings under low loads are particularly prone to slippage
In order to prevent slippage damage, the bearing must be subjected to a minimum axial load Fa min ➤ Equation. In vertical bearing arrangements in particular, the requisite minimum axial load Fa min is normally achieved, however, simply by the weight of the bearing parts and the external forces. If this is not the case, the bearing arrangement must be preloaded, for example by means of springs or a shaft nut ➤ section.
Minimum axial load
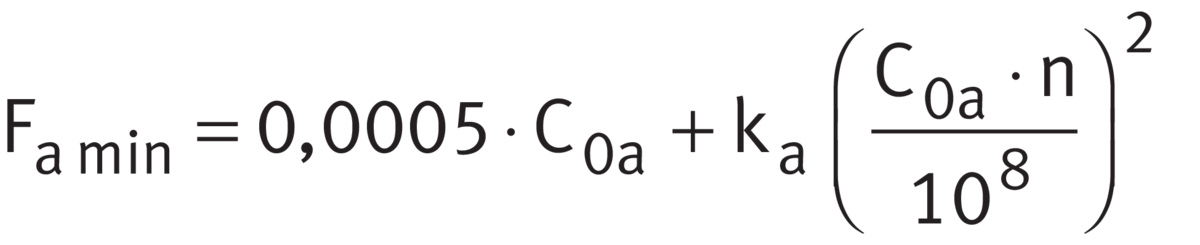
Legend
Fa min | N |
Minimum axial load |
C0a | N |
Basic static load rating, axial |
ka |
Factor for determining the minimum load; ka = 3 |
|
n | min–1 |
Speed. |
Design of bearing arrangements
Design of adjacent parts
Axial needle roller bearings cannot tolerate angular misalignments ➤ section. The locating surfaces for the bearing parts on the shaft and in the housing must therefore be vertical to the shaft axis, while the adjacent parts must be rigid and flat. They must be configured such that the bearing washers are supported as far as possible over the whole circumference and over the whole raceway width.
Contact surfaces of rolling elements in direct bearing arrangements with needle roller and cage assemblies
Produce the running surfaces as a rolling bearing raceway
For the very smallest axial design space, axial needle roller and cage assemblies can also run directly (i. e. without axial bearing washers) on the adjacent construction. In this case – and if the load carrying capacity of the axial needle roller and cage assemblies is to be fully utilised – the raceways on the shaft and in the housing must be produced as a rolling bearing raceway or must correspond to the quality and hardness of axial bearing washers. When designing the raceway on the shaft and in the housing, the raceway dimensions Eaand Eb of axial needle roller and cage assemblies must be observed ➤ dimension table. If the values are observed, this will ensure that the raceways for the needle rollers – taking account of any possible axial offset of the needle roller and cage assembly – are adequately dimensioned.
Raceway design
Design of contact faces:
- raceway hardness 670 HV to 840 HV
- radial cage guidance surfaces Ramax 0,8 (Rzmax 4)
- roughness Ramax 0,2 (Rzmax 1)
- raceway dimensions Ea and Eb according to the product tables must be observed
- total axial runout tolerances to ISO tolerance grade IT5 (for special requirements IT4) relative to the inside diameter of the axial needle roller and cage assemblies Dc1 must be observed.
Tolerances for shaft and housing bore
Proven tolerances are given in ➤ Table . If the data are observed, this will give correct radial guidance of the bearing elements.
Tolerances for shafts and housing bores
Bearing component |
Tolerance class for |
||
---|---|---|---|
Shaft |
Bore |
||
AXK |
Shaft guided |
h8 |
‒ |
AS |
Externally centred |
Shaft released |
H9 |
Internally centred |
h8 |
Bore released |
- The envelope requirement Ⓔ applies.
Tolerances for the centring spigot in the housing bore
Where axial needle roller bearings AXW are to be combined with drawn cup needle roller bearings with open ends or closed end, or with needle roller bearings, the bore tolerances selected for the bore of the centring spigot in the housing must be the same as for the radial bearings ➤ section, ➤ Figure and ➤ Figure.
Release and guidance of bearing parts
Release of shaft and housing locating washers
If the bearing washers are centred on the shaft, they must have radial clearance in the housing bore while, if they are centred in the housing, there must be radial clearance between the washer bore and the shaft ➤ Table.
Guidance of axial needle roller and cage assemblies
In order to achieve the lowest possible sliding speeds on the guidance surfaces, the axial needle roller and cage assemblies are generally guided on the shaft. This is particularly important in the case of high speeds.
Mounting and dismounting
The mounting and dismounting options for the bearings must be taken into consideration in the design of the bearing position.
As the bearings are not self-retaining, they are easy to mount
Axial needle roller bearings are not self-retaining. As a result, the bearing parts can be mounted separately from each other. This gives simplified mounting of the bearings.
Mounting position of bearing washers
The axial bearing washers AS must be suitable as a raceway on both sides, i. e. either side of the washer can face towards the needle rollers.
Schaeffler Mounting Handbook
Rolling bearings must be handled with great care
Rolling bearings are well-proven precision machine elements for the design of economical and reliable bearing arrangements, which offer high operational security. In order that these products can function correctly and achieve the envisaged operating life without detrimental effect, they must be handled with care.
The Schaeffler Mounting Handbook MH 1 gives comprehensive information about the correct storage, mounting, dismounting and maintenance of rotary rolling bearings http://www.schaeffler.de/std/1B68. It also provides information which should be observed by the designer, in relation to the mounting, dismounting and maintenance of bearings, in the original design of the bearing position. This book is available from Schaeffler on request.
Legal notice regarding data freshness
The further development of products may also result in technical changes to catalogue products
Of central interest to Schaeffler is the further development and optimisation of its products and the satisfaction of its customers. In order that you, as the customer, can keep yourself optimally informed about the progress that is being made here and with regard to the current technical status of the products, we publish any product changes which differ from the printed version in our electronic product catalogue.
We therefore reserve the right to make changes to the data and illustrations in this catalogue. This catalogue reflects the status at the time of printing. More recent publications released by us (as printed or digital media) will automatically precede this catalogue if they involve the same subject. Therefore, please always use our electronic product catalogue to check whether more up-to-date information or modification notices exist for your desired product.
Further information
In addition to the data in this chapter, the following chapters in Technical principles must also be observed in the design of bearing arrangements: