Lubrication
Basic principles
Lubrication and maintenance are important for the reliable operation and long operating life of rolling bearings.
Functions of the lubricant
The lubricant should:
- form a lubricant film on the contact surfaces that is sufficiently capable of supporting loads and thus preventing wear and premature fatigue
- dissipate heat in the case of oil lubrication
- give additional sealing of the bearing, in the case of grease lubrication, against the entry of both solid and fluid contaminants
- dampen running noise
- give protection against corrosion
Selection of the type of lubrication
Oil or grease lubrication
It should be determined as early as possible in the design process whether bearings should be lubricated using grease or oil.
The following factors are decisive in determining the type of lubrication and quantity of lubricant:
- the operating conditions
- the type and size of the bearing
- the adjacent construction
- the lubricant feed
Grease lubrication
Criteria for grease lubrication
In the case of grease lubrication, the following criteria must be considered:
- very little design work required
- the sealing action
- the reservoir effect
- long operating life with little maintenance work (lifetime lubrication possible in certain circumstances)
- if relubrication is required, it may be necessary to provide collection areas for old grease and feed ducts
- no heat dissipation by the lubricant
- no rinsing out of wear debris and other particles
Oil lubrication
Criteria for oil lubrication
In the case of oil lubrication, the following criteria must be considered:
- good lubricant distribution and supply to contact areas
- dissipation of heat possible from the bearing (significant principally at high speeds and/or loads)
- rinsing out of wear debris
- very low friction losses with minimal quantity lubrication
- more work required on feed and sealing
Under extreme operating conditions (such as very high temperatures, vacuum, aggressive media), it may be possible to use special lubrication methods such as solid lubricants in consultation with Schaeffler.
Design of lubricant feeds
Observe guidelines
The feed lines and lubrication holes in the housings and shafts ➤ Figure and ➤ Figure.
- should lead directly to the lubrication hole in the rolling bearing
- should be as short as possible
A separate feed must be provided for each bearing. Ensure that the feed lines are filled ➤ Figure; the feed line should be bled if necessary. Follow the instructions provided by the lubrication device manufacturer.
Lubricant feed lines |
![]() |
Arrangement of feed lines to more than one bearing on a shaft |
![]() |
Further information
Comprehensive information on the lubrication of rolling bearings is contained in Technical Product Information TPI 176. This publication can be requested from Schaeffler.
Grease lubrication
Greases can be differentiated in terms of their thickeners of varying composition and base oils. The base oils of greases are covered by the information in the section Oil lubrication ➤ link.
Composition of a grease
Conventional greases have metal soaps as thickeners and a mineral base oil ➤ Figure. They also contain additives. These have a specific influence on, for example, the characteristics in relation to wear prevention, corrosion prevention or resistance to ageing. These combinations of additives are not, however, fully effective across every temperature and load range.
Greases exhibit widely varying behaviour in response to environmental influences such as temperature and moisture.
Type of grease
|
![]() |
Lubricants must always be checked for their compatibility with:
- other lubricants
- anti-corrosion agents
- thermoplastics, thermosets and elastomers
- light and non-ferrous metals
- coatings
- colouring agents and paints
- and the environment. When considering compatibility with the environment, attention must be paid to toxicity, biodegradability and water pollution class
Type of grease
The characteristics of a grease are dependent on:
- the base oil
- the viscosity of the base oil (this is significant for the speed range)
- the thickener (the shear strength is significant for the speed range)
- the additives
Consistency of greases
Greases are subdivided into consistency classes (NLGI classes to DIN 51818). For rolling bearings, classes 1, 2, 3 should be used in preference ➤ Figure.
Consistency of greases NLGI classes |
![]() |
Selection of suitable grease
The grease is determined by the operating conditions
Rolling bearing greases K to DIN 51825 are suitable.
Greases should be selected in accordance with the operating conditions of the bearing:
Operating temperature range
The grease must correspond to the operating temperatures
The operating temperature range of the grease must correspond to the range of possible operating temperatures in the rolling bearing.
Grease manufacturers indicate an operating temperature range for their rolling bearing greases K to DIN 51825.
The upper value is determined in accordance with DIN 51821 by means of testing on the FAG rolling bearing grease test rig FE9. At the upper operating temperature, a 50% failure probability rate (F50) of at least 100 hours must be achieved in this test.
The lower value is defined in accordance with DIN 51825 by means of flow pressure. The flow pressure of a grease is the pressure required to press a stream of grease through a defined nozzle. For greases of type K, the flow pressure at the lower operating temperature must be less than 1 400 mbar.
The use of flow pressure in determining the lower operating temperature only indicates, however, whether the grease can be moved at this temperature. This cannot be used to give an indication of its suitability for use in rolling bearings at low temperatures.
In addition to the lower operating temperature of a grease, therefore, the low temperature frictional torque is also determined in accordance with ASTM D 1478or IP 186/93. At the lower operating temperature, the starting torque must not exceed 1 000 Nmm and the running torque must not exceed 100 Nmm.
Schaeffler recommends that greases should be used in accordance with the bearing temperature normally occurring in the standard operating range, in order to achieve a reliable lubricating action and an acceptable grease operating life ➤ Figure.
At low temperatures, greases release very little base oil. This can result in lubricant starvation. Schaeffler therefore recommends that greases are not used below the lower continuous limit temperature ϑlower limit on a permanent basis ➤ Figure. This is approx. 20 K above the lower operating temperature of the grease as stated by the grease manufacturer.
The upper continuous limit temperature ϑupper limit must not be exceeded if a temperature-induced reduction in the grease operating life is to be avoided; see Grease operating life ➤ link.
At consistently low temperatures (for example in cold store applications), it must be ensured that the grease releases sufficient oil in relation to the bearing type.
Operating temperature range ϑ = operating temperature ΔT = temperature difference
|
![]() |
Pressure properties
The pressure properties are dependent on the viscosity
The viscosity at operating temperature must be sufficiently high for the formation of a lubricant film capable of supporting loads. At high loads, greases with EP characteristics (“extreme pressure”) and high base oil viscosity should be used (KP grease to DIN 51825). Such greases should also be used for bearings with substantial sliding or line contact.
Silicone greases should only be used at low loads (P ≦ 0,03 · C).
Greases with solid lubricants should preferably be used for applications with mixed or boundary friction conditions. The solid lubricant particle size must not exceed 5 μm.
Speed
Speed parameter n · dM is a criterion for grease selection
Greases should be selected in accordance with the speed parameter n · dM for grease ➤ Table:
- For rolling bearings running at high speeds or with a low starting torque, greases with a high speed parameter should be used
- For bearings running at low speeds, greases with a low speed parameter should be used
Under centrifugal accelerations > 500 · g, separation (of the thickener and base oil) may occur. In this case, please consult the lubricant manufacturer.
The consistency of polycarbamide greases can be altered by shear stresses to a greater extent than that of metal soap greases.
Water and moisture
Water reduces the operating life
Water in the grease has a highly detrimental effect on the operating life of bearings:
- the static behaviour of greases in the presence of water is assessed in accordance with DIN 51807 ➤ Figure
- the anti-corrosion characteristics can be tested according to DIN 51802 (Emcor test) – information is given in the grease manufacturer’s data sheets
Behaviour in the presence of water in accordance with DIN 51807
|
![]() |
Grease operating life
The grease operating life tfG applies where this is below the calculated bearing life and the bearings are not lubricated.
A guide value can be determined in approximate terms in accordance with ➤ Equation:
Guide value for grease operating life

Legend
tfG | h |
Guide value for grease operating life |
tf | h |
Basic grease operating life |
KT, KP, KR, KU |
- |
Correction factors for temperature, load, oscillation and environment |
If a grease operating life > 3 years is required, this must be agreed in consultation with the lubricant manufacturer.
Guidelines on calculating the grease operating life ➤ link.
Basic grease operating life
This applies under the preconditions according to ➤ Table.
Preconditions for the basic grease operating life
Precondition |
|
---|---|
Bearing temperature |
< upper continuous limit temperature ϑupper limit |
Load ratio |
C0/P = 20 |
Speed and load |
Constant |
Load in main direction |
Radial in radial bearings, axial in axial bearings |
Axis of rotation |
Horizontal for radial bearings |
Inner ring |
Rotating |
Environmental influences |
No disruptive influences |
The basic grease operating life tf is dependent on the bearing-specific speed parameter kf · n · dM and is calculated using ➤ Figure.
Legend
kf | - |
Bearing type factor ➤ Table |
n | min–1 |
Operating speed or equivalent speed |
dM | mm |
Mean bearing diameter (d + D)/2 |
Calculation of basic grease operating life
Calculation of basic grease operating life tf = basic grease operating life kf · n · dM = bearing-specific speed parameter |
![]() |
Factor kf – as a function of bearing type
Bearing type |
Factor kf |
---|---|
Deep groove ball bearings, single row, Generation C |
0,8 |
Deep groove ball bearings, single row |
1 |
Deep groove ball bearings, double row |
1,5 |
Angular contact ball bearings, single row |
1,6 |
Angular contact ball bearings, single row, X-life |
1,3 |
Angular contact ball bearings, double row |
2 |
Angular contact ball bearings, double row, X-life |
1,6 |
Spindle bearings, α = 15° |
0,75 |
Spindle bearings, α = 25° |
0,9 |
Four point contact bearings |
1,6 |
Four point contact bearings, X-life |
1,3 |
Self-aligning ball bearings |
1,45 |
Axial deep groove ball bearings |
5,5 |
Axial angular contact ball bearings, single row |
1,8 |
Axial angular contact ball bearings, double row |
2 |
Cylindrical roller bearings, single row |
2 |
Cylindrical roller bearings LSL, ZSL |
3 |
Cylindrical roller bearings, double row |
3 |
Cylindrical roller bearings, full complement |
6 |
Tapered roller bearings |
4 |
Spherical roller bearings |
8 |
Toroidal roller bearings TORB |
8 |
Needle roller and cage assemblies, needle roller bearings |
3,6 |
Drawn cup needle roller bearings |
4,2 |
Yoke type track rollers, stud type track rollers with cage, stud type track rollers with full complement cylindrical roller set |
20 |
Yoke type track rollers, stud type track rollers, |
40 |
Ball bearing type track rollers, single row |
1 |
Ball bearing type track rollers, double row |
2 |
Yoke type track rollers PWTR, stud type track rollers PWKR |
6 |
Crossed roller bearings |
4,4 |
Axial needle roller bearings, axial cylindrical roller bearings |
58 |
Radial insert ball bearings, housing units |
1 |
Guidelines on calculating the grease operating life
Combined rolling bearings
The radial and axial bearing components must be calculated separately; the decisive value is the shorter grease operating life.
Rotating outer ring
If the outer ring rotates, there may be a reduction in the grease operating life.
In the case of yoke and stud type track rollers:
- the angular misalignment must be zero
- the effect of the rotating outer ring on the grease operating life is taken into consideration in the bearing type factor kf
Restrictions of the calculation
The grease operating life cannot be determined using the method described in the following cases:
- if the grease can leave the bearing arrangement
- there is excessive evaporation of the base oil
- in bearing positions without seals
- in axial bearings with a horizontal axis of rotation
- if air is sucked into the rolling bearing during operation
- this can cause the grease to oxidise
- for bearing arrangements that have a vertical shaft
- in combined rotary and linear motion (the grease is distributed over the whole stroke length)
- if contamination, water or other fluids enter the bearing
- for spindle bearings
- for drawn cup roller clutches
- for screw drive bearings
- for high precision bearings for combined loads
- for super precision cylindrical roller bearings NN30
The additional guidelines on lubrication in the product chapters must be observed.
Correction factors for determining the grease operating life
Temperature factor KT
If the bearing temperature is higher than the reference temperature ϑreference, KT must be determined from the diagram ➤ Figure.
The diagram must not be used if the bearing temperature is higher than the upper operating temperature of the grease used ➤ Table. If necessary, a different grease must be selected or contact must be made with Schaeffler.
Depending on the grease quality, temperature factors KT > 1 are also possible below the reference temperature.
Temperature factor KT = temperature factor
|
![]() |
Load factor KP
The factor KP is dependent on the bearing and describes the reduction at higher load (this places greater strain on the grease) ➤ Figure and ➤ Table.
Load correction factor Kp Kp = load correction factor C0/P = ratio between basic static load rating and equivalent dynamic bearing load See: |
![]() |
Correction factor for load KP
Curve |
Bearing type |
---|---|
|
Axial angular contact ball bearings, double row |
|
Axial deep groove ball bearings |
![]() |
Axial needle roller bearings, axial cylindrical roller bearings |
|
Crossed roller bearings |
|
Spherical roller bearings with central rib |
|
Needle roller and cage assemblies, needle roller bearings |
|
Drawn cup needle roller bearings |
|
Cylindrical roller bearings, double row (excluding NN30) |
![]() |
Yoke type track rollers PWTR, stud type track rollers PWKR |
|
Yoke and stud type track rollers with cage, full complement cylindrical roller set |
|
Yoke and stud type track rollers, full complement needle roller set |
|
Four point contact bearings |
|
Cylindrical roller bearings LSL, ZSL |
|
Cylindrical roller bearings, full complement |
|
Cylindrical roller bearings, single row (constant or alternating load) |
|
Tapered roller bearings |
|
Barrel roller bearings |
|
Spherical roller bearings without central rib (E1) |
|
Toroidal roller bearings |
|
Deep groove ball bearings (single or double row) |
![]() |
Angular contact ball bearings (single or double row) |
|
Self-aligning ball bearings |
|
Ball bearing track rollers (single or double row) |
|
Radial insert ball bearings, housing units |
Oscillation factor KR
The factor KR applies for an angle of oscillation φ < 180° ➤ Figure. Oscillating motion places a greater strain on the grease than does rotating motion.
In order to reduce fretting corrosion, the lubrication interval should be reduced.
If the rolling elements do not undergo complete rotation, please consult Schaeffler.
Correction factor for oscillation KR KR = correction factor for oscillation φ = angle of oscillation
|
![]() |
Environmental factor KU
The factor KU takes account of the influences of moisture, shaking forces, slight vibration (leading to fretting corrosion) and shocks ➤ Table. It does not take account of extreme environmental influences such as water, aggressive media, contamination, radiation and extreme vibrations such as those occurring in vibratory machines.
In relation to contamination, the influence of contamination on rating life calculation must also be noted.
Environment factor KU
Environmental influence |
Factor KU |
---|---|
Slight (e. g. test rig) |
1 |
Moderate (standard) |
0,8 |
Heavy (e. g. outdoor application) |
0,5 |
Relubrication intervals
Observe lubrication intervals
Where rolling bearings are relubricated, attention must be paid to the lubrication interval in order to ensure reliable function of the bearings.
The precise lubrication interval should be determined by tests conducted under application conditions. To do this:
- sufficiently long observation periods must be used
- the condition of the grease must be checked at regular intervals
For reasons of operational reliability, relubrication intervals of > 1 year are not recommended.
Lubrication interval guide value
Experience shows that the guide value for most applications is ➤ Equation.
Guide value for relubrication interval

Legend
tfR | h |
Guide value for relubrication interval |
tfG | h |
Guide value for grease operating life |
Relubrication conditions
The grease used for relubrication must be the same as that used in initial greasing. If other greases are used, the miscibility and compatibility of the greases must be checked.
Relubrication quantity
Due to the compact construction of the bearings, relubrication should be carried out using 50% to 80% of the initial greasing quantity (recommendation).
If feed lines filled with air are present, the filling volume of the feed lines should be included in calculation of the relubrication quantity.
Relubrication
Relubrication should always be carried out as follows:
- with the bearing still warm from operation and rotating if safe to do so
- before the bearing comes to rest if safe to do so
- before extended breaks in operation
Relubrication should continue until a fresh collar of grease appears at the seal gaps. Old grease must be allowed to leave the bearing unhindered.
Grease reservoir
The initial greasing quantity is between 30% and 100% of the available volume in the bearing, dependent on the bearing type and operating conditions.
A grease reservoir can extend the grease operating life. The grease in the reservoir must be in constant contact with the grease on the raceway. The grease operating life does not increase proportionally with the size of the grease reservoir.
The volume of the grease reservoir should correspond to the volume in the bearing between the inner and outer ring (not taking account of the cage and rolling elements) ➤ Figure and ➤ Figure.
Evaporation of the base oil should be prevented by design measures, for example by sealing shields ➤ Figure and ➤ Figure.
Grease reservoir on one side
|
![]() |
Grease reservoir on both sides
|
![]() |
Miscibility
Preconditions
Mixtures of greases should be avoided if at all possible. If they are unavoidable, the following preconditions must be fulfilled:
- The base oil must be the same
- The thickener types must match
- The base oil viscosities must be similar (they must not differ by more than one ISO VG class )
- The consistency must be identical (NLGI class)
Miscibility of greases must always be agreed in consultation with the lubricant manufacturer.
Even when these preconditions are fulfilled, impairment of the performance capability of the mixed grease cannot be ruled out.
If a decision is taken to change to a different grease grade, the grease should be rinsed out if this is possible. Further relubrication should be carried out after a shortened period.
If incompatible greases are mixed, this can lead to considerable structural changes. Substantial softening of the grease mixture may also occur. Definite statements on miscibility can only be obtained by means of suitable tests.
Storage life
In general, the greases can be stored for 3 years.
Preconditions
The preconditions are:
- a closed room or store
- temperatures between 0 °C and +40 °C
- relative humidity no more than 65%
- no influence of chemical agents (vapours, gases, fluids)
- the rolling bearings are sealed
Lubricants age due to environmental influences. The information provided by lubricant manufacturers must always be observed.
After long periods of storage, the start-up frictional torque of greased bearings can be temporarily higher than normal. The lubricity of the grease may also have deteriorated.
Since the lubrication characteristics of greases vary and different raw materials may be used for greases of the same name, Schaeffler cannot offer any guarantees either for the lubricants used by customers for relubrication or for their characteristics.
Oil lubrication
Mineral oils or synthetic oils are suitable
For the lubrication of rolling bearings, mineral oils and synthetic oils are essentially suitable. Oils with a mineral oil base are used most frequently. They must, as a minimum, fulfil the requirements in accordance with DIN 51517 or DIN 51524.
Special oils, often synthetic oils, are used under extreme operating conditions or where there are special requirements relating to oil resistance. In these cases, please consult the lubricant manufacturers or Schaeffler.
Operating temperatures
The information provided by the lubricant manufacturer should be taken as authoritative.
Selection of suitable oil
The achievable bearing life and security against wear are higher with better separation of the contact surfaces by a lubricant film ➤ Figure.
Lubricant film in the contact zones hmin = minimum lubricant film thickness
|
![]() |
Reference viscosity for mineral oils
Guide value for ν1
The guide value for ν1 is dependent on the mean bearing diameter dM and the speed n. It takes account of the EHD theory of lubricant film formation and practical experience.
Depending on the operating speed, the oil at operating temperature must have at least the reference viscosity ν1 ➤ Figure and ➤ Figure.
Calculating the reference viscosity ν1 ν1 = reference viscosity dM = mean bearing diameter n = speed |
![]() |
ν/ϑ diagram for mineral oils ν = operating viscosity ϑ = operating temperature ν40 = viscosity at +40 °C |
![]() |
Calculation of reference viscosity
Determine ν1
The reference viscosity ν1 is calculated as follows:
- Allocate ν1 to a nominal viscosity between ISO VG 10 and ISO VG 1500 (mid‑point viscosity in accordance with ISO 3448)
- Round intermediate values to the nearest ISO VG (due to the steps between groups)
This method cannot be used for synthetic oils, since these have different V/P (viscosity/pressure) and V/T (viscosity/temperature) characteristics. In these cases, please consult Schaeffler.
Influence of temperature on viscosity
Aim for VI of 95
As the temperature increases, the viscosity of the oil decreases. This temperature-dependent change in the viscosity is described using the viscosity index VI. For mineral oils, the viscosity index should be at least 95.
When selecting the viscosity, the lower operating temperature must be taken into consideration, since the increasing viscosity will reduce the flowability of the lubricant. As a result, the level of power losses may increase.
Viscosity ratio κ
A very long life can be achieved with a viscosity ratio κ = ν/ν1 = 3 to 4 (ν = operating viscosity). Highly viscous oils do not, however, bring only advantages. In addition to the power losses arising from lubricant friction, there may be problems with the feed and removal of oil at low or even at normal temperatures.
Aim for long fatigue life
The oil selected must be sufficiently viscous that it gives the highest possible fatigue life. It must also be ensured that the bearings are always supplied with adequate quantities of oil.
Pressure properties and anti-wear additives
Oils with wear additives
If the bearings are subjected to high loads or if the operating viscosity ν is less than the reference viscosity ν1, oils with anti-wear additives (type P in accordance with DIN 51502) should be used. Such oils are also necessary for rolling bearings with a substantial proportion of sliding contact (for example, bearings with line contact). These additives form boundary layers to reduce the harmful effects of metallic contact occurring at various points (wear).
The suitability of these additives varies and is normally heavily dependent on temperature. Their effectiveness can only be assessed by means of testing in the rolling bearing (for example on our test rig FE8 to DIN 51819).
Silicone oils should only be used for low loads (P ≦ 0,03 · C).
Compatibility
Check compatibility prior to use
Before an oil is used, its behaviour must be checked in relation to plastics, seal materials (elastomers) and light and non-ferrous metals. This must always be checked under dynamic loading and at operating temperature.
Synthetic oils must always be checked for their compatibility. The lubricant manufacturer must be consulted on this at the same time.
Miscibility
Avoid mixing different oils
The mixing of different oils should be avoided wherever possible. In particular, the presence of different additive packages may lead to undesirable interactions.
In general, oils with a mineral oil base and the same classification are miscible, for example type HLP with type HLP. The viscosities should vary by no more than one ISO VG class.
Synthetic oils must always be checked for their compatibility. The lubricant manufacturer must be consulted on this at the same time.
Miscibility must be checked in advance for each individual case.
Cleanliness
An oil filter should be used
The cleanliness of the oil has a considerable influence on the rating life of the bearings. Schaeffler therefore recommends that an oil filter should be provided; attention must be paid to the filtration rate. The filter mesh should be < 25 μm.
Lubrication methods
Proven methods
The essential lubrication methods are:
- drip feed oil lubrication
- pneumatic oil lubrication (to protect the environment, this should be used as a substitute for oil mist lubrication)
- oil bath lubrication (immersion or sump lubrication)
- recirculating oil lubrication
Drip feed oil lubrication
This is suitable for bearings running at high speeds ➤ Figure. The oil quantity required is dependent on the type and size of bearing, the operating speed and the load. The guide value is between 3 drops/min and 50 drops/min for each rolling element raceway (one drop weighs approx. 0,025 g).
Excess oil must be allowed to flow out of the bearing arrangement.
Drip feed oil lubrication |
![]() |
Pneumatic oil lubrication
This method is particularly suitable for radial bearings running at high speeds and under low loads (n · dM = 800 000 to 3 000 000 min–1 · mm) ➤ Figure. Clean compressed air free from moisture feeds oil to the bearing. This generates an excess pressure, which prevents contaminants from entering the bearing.
With a pneumatic oil lubrication system designed for minimal quantity lubrication, low frictional torque and a low operating temperature can be achieved.
Parameters
Parameters for design of the lubrication system should be requested from the equipment manufacturers.
Pneumatic oil lubrication of axial bearings should be avoided if possible.
The oil quantity required for adequate supply is dependent on the bearing type.
Pneumatic oil lubrication has little cooling effect.
Follow the instructions provided by the manufacturers of the lubrication systems.
Pneumatic oil lubrication
|
![]() |
Oil bath lubrication
The oil level should reach the centre line of the lowest rolling element ➤ Figure. If the oil level is higher than this, the bearing temperature may increase at high circumferential velocities (with losses due to splashing). Furthermore, foaming of the oil may occur.
n · dM values
In general, it is suitable for speeds up to n · dM = 300 000 min–1 · mm. At n · dM < 150 000 min–1 · mm, the bearing may be completely immersed.
In bearings with an asymmetrical cross-section, oil return ducts must be provided due to the pumping effect so that recirculation can be achieved.
Axial bearings
In axial bearings, the oil level must cover the inside diameter of the axial cage.
Proportion oil quantity adequately
The oil quantity in the housing must be adequately proportioned, as otherwise very short oil change intervals will be necessary.
Oil bath lubrication
|
![]() |
Recirculating oil lubrication
In recirculating oil lubrication, the oil is subjected to additional cooling ➤ Figure. The oil can therefore dissipate heat from the bearing. The quantity of oil required for heat dissipation is dependent on the cooling conditions.
Recirculating oil lubrication
|
![]() |
Oil quantity
The oil quantities are matched to the operating conditions ➤ Figure. The diagram indicates oil quantities that can be fed through the bearing without pressure with a side feed arrangement and banking up to the lower edge of the shaft.
Bearings with asymmetrical cross-section
For bearings with an asymmetrical cross-section (such as angular contact ball bearings, tapered roller bearings, axial spherical roller bearings), larger throughput quantities are permissible due to the pumping effect than for bearings with a symmetrical cross-section. Large quantities can be used to dissipate wear debris or heat.
Oil quantities
D = outside bearing diameter a = oil quantity sufficient for lubrication b = upper limit for bearings of symmetrical design c = upper limit for bearings of asymmetrical design
|
![]() |
Design of adjacent construction for oil lubrication
The lubrication holes in the housing and shaft must align with those in the rolling bearings. Adequate cross-sections must be provided for annular slots, pockets, etc. The oil must be able to flow out without pressure (this prevents oil build-up and additional heating of the oil).
Axial bearings
In axial bearings, the oil must always be fed from the inside to the outside.
Guide values
The cross-section of the oil outlet hole should be significantly larger than that of the inlet ➤ Figure.
The cross-section Arab is dependent on the oil quantity and the viscosity ➤ Equation.
Outlet cross section

Legend
Arab | mm2 |
Outlet cross-section taking account of viscosity |
Kab | - |
Correction factor for viscosity ➤ Table |
Aab | mm2 |
Outlet cross-section ➤ Figure |
Outlet cross-section (guide values) Aab = cross-section for pressure-free oil runout
|
![]() |
Correction factor Kab
Viscosity |
Factor |
||
---|---|---|---|
ν |
Kab |
||
mm2/s |
|||
from |
to |
from |
to |
‒ |
30 |
1 |
‒ |
30 |
60 |
1,2 |
1,6 |
60 |
90 |
1,8 |
2,2 |
90 |
120 |
2,4 |
2,8 |
120 |
150 |
3 |
3,4 |
Oil injection lubrication
Advantages and disadvantages
In bearings running at high speeds, the oil is injected into the gap between the cage and bearing ring ➤ Figure. Injection lubrication using large recirculation quantities is associated with high power loss.
Heating of the bearings can only be held within limits with a considerable amount of effort. The appropriate upper limit for the speed parameter n · dM = 1 000 000 min-1 · mm for recirculating lubrication with suitable bearings (for example spindle bearings) can be exceeded to a considerable degree when using injection lubrication.
Oil injection lubrication
|
![]() |
Heat dissipation by the lubricant
Values L and
L can be calculated
Oil can dissipate frictional heat from the bearing. It is possible to calculate the heat flow L that is dissipated with the lubricant and the necessary lubricant volume flow
L.
Heat flow
The total dissipated heat flow due to possible heating by an external source can be calculated using ➤ Equation, while the heat flow dissipated by the lubricant can be calculated using ➤ Equation.
Total dissipated heat flow

Heat flow dissipated by the lubricant

Legend
![]() |
kW |
Total dissipated heat flow |
n | min-1 |
Operating speed or equivalent speed |
M0 | Nmm |
Frictional torque as a function of speed |
M1 | Nmm |
Frictional torque as a function of load |
![]() |
kW |
Heat flow due to heating by external source |
![]() |
kW |
Heat flow dissipated by the lubricant |
![]() |
kW |
Heat flow dissipated via the bearing seating surfaces |
Lubricant volume flow
The lubricant volume flow can be calculated approximately ➤ Equation.
Lubricant volume flow
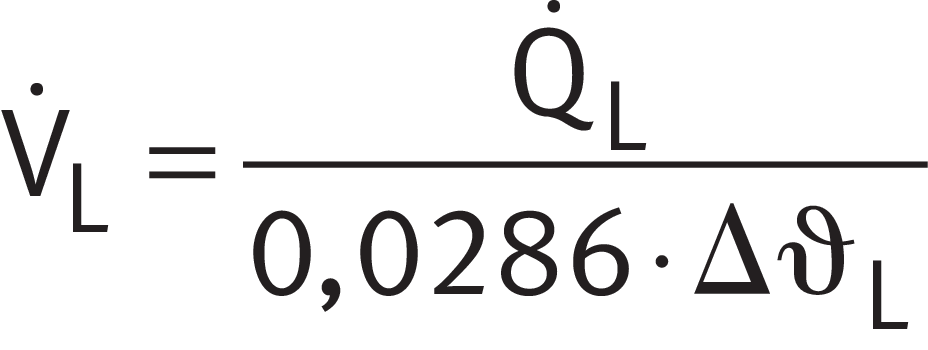
Legend
|
l/min |
|
![]() |
kW |
Heat flow dissipated by the lubricant |
ΔϑL | K |
Difference between oil inlet temperature and oil outlet temperature |
Guide values
If these values cannot be calculated, the guide values according to ➤ Figure apply for the temperature difference of ΔϑL = 10 K.
Guide values for the oil quantity in cooling and lubrication NR = frictional power
|
![]() |
Oil changes
One oil change per year is usually sufficient
At temperatures in the bearing of less than +50 °C and with only slight contamination, an oil change once per year is generally sufficient. Guide values for oil change intervals are given in ➤ Figure. The precise oil change intervals should be agreed in consultation with the oil manufacturer.
Severe operating conditions
Under severe conditions, the oil should be changed more frequently. This applies, for example, in the case of higher temperatures and low oil quantities with a high circulation index. The circulation index indicates how often the entire oil volume available is recirculated or pumped per hour ➤ Equation.
Circulation index

Oil change intervals ϑ = oil sump temperature t = oil change interval
|
![]() |
Lubricating greases
Greases
Designation3) |
Classification |
Type of grease |
Operating temperature range |
Upper continuous limit temperature ϑupper limit1) |
Designation |
NLGI class |
Speed parameter n · dM |
ISO VG class (base oil)2) |
Designation3) |
Recommended Arcanol grease for relubrication |
|||
---|---|---|---|---|---|---|---|---|---|---|---|---|---|
°C |
°C |
min-1 · mm |
|||||||||||
from |
to |
from |
to |
from |
to |
||||||||
GA01 |
Ball bearing grease for ϑ < +180 °C |
Polycarbamide Ester oil |
–30 |
+180 |
+125 |
GA01 |
2 |
3 |
600 000 |
68 |
220 |
GA01 |
‒ |
GA02 |
Ball bearing grease for ϑ < +160 °C |
Polycarbamide SHC |
–40 |
+160 |
+90 |
GA02 |
2 |
3 |
500 000 |
68 |
220 |
GA02 |
‒ |
GA13 |
Standard ball bearing and insert bearing grease for D > 62 mm |
Lithium soap Mineral oil |
–20 |
+120 |
+75 |
GA13 |
3 |
‒ |
500 000 |
68 |
150 |
GA13 |
Multi2 |
GA14 |
Low-noise ball bearing grease for D ≦62 mm |
Lithium soap Mineral oil |
–30 |
+120 |
+75 |
GA14 |
2 |
‒ |
500 000 |
68 |
150 |
GA14 |
Multi2 |
GA15 |
Low-noise ball bearing grease for high speeds |
Lithium soap Ester oil/SHC |
–40 |
+120 |
+75 |
GA15 |
2 |
3 |
1 000 000 |
22 |
32 |
GA15 |
‒ |
GA22 |
Free-running grease with low frictional torque |
Lithium soap Ester oil, mineral oil |
–50 |
+120 |
+70 |
GA22 |
2 |
‒ |
1 500 000 |
10 |
22 |
GA22 |
‒ |
L069 |
Insert bearing grease for wide temperature range |
Polycarbamide Ester oil |
–40 |
+180 |
+120 |
L069 |
2 |
‒ |
700 000 |
68 |
220 |
L069 |
‒ |
GA08 |
Grease for line contact |
Lithium complex soap Mineral oil |
–20 |
+140 |
+95 |
GA08 |
2 |
3 |
500 000 |
150 |
320 |
GA08 |
Load150 |
GA26 |
Standard grease for drawn cup roller clutches |
Calcium/lithium soap Mineral oil |
–20 |
+80 |
+60 |
GA26 |
2 |
‒ |
500 000 |
10 |
22 |
GA26 |
‒ |
GA28 |
Screw drive bearing grease |
Lithium soap Synthetic oil/mineral oil |
–30 |
+140 |
+80 |
GA28 |
2 |
‒ |
800 000 |
15 |
100 |
GA28 |
Multitop |
GA11 |
Rolling bearing grease resistant to media for temperatures up to +250 °C |
PTFE Alkoxyfluoroether |
–30 |
+260 |
+200 |
GA11 |
2 |
‒ |
300 000 |
460 |
680 |
GA11 |
Temp200 |
GA47 |
Rolling bearing grease resistant to media for temperatures up to +140 °C |
Barium complex soap Mineral oil |
–20 |
+130 |
+70 |
GA47 |
1 |
2 |
350 000 |
150 |
320 |
GA47 |
‒ |
- The upper continuous limit temperature ϑupperlimit must not be exceeded if a reduction in the grease operating life due to temperature is to be avoided.
- Dependent on bearing type.
- GA.. Stands for Grease Application Group.., based on Grease Spec 00.
Arcanol rolling bearing greases
Arcanol rolling bearing greases
Grease |
Characteristic applications |
Operating temperature |
Continuous limit |
Thickener |
Base oil |
Grease |
Consistency |
Base oil viscosity at +40 °C |
Temperatures |
Low friction, high speed |
High load, low speed |
Vibrations |
Support for seals |
Relubrication facility |
Grease |
|||
---|---|---|---|---|---|---|---|---|---|---|---|---|---|---|---|---|---|---|
°C |
°C |
NLGI |
mm2/s |
|||||||||||||||
from |
to |
Low |
High |
|||||||||||||||
Multi-purpose greases |
Multitop |
|
–501) |
+140 |
+80 |
Lithium soap |
Partially synthetic oil |
Multitop |
2 |
82 |
+++ |
++ |
++ |
+++ |
++ |
+ |
+++ |
Multitop |
Multi-purpose greases |
Multi2 |
|
–30 |
+120 |
+75 |
Lithium soap |
Mineral oil |
Multi2 |
2 |
110 |
++ |
+ |
+ |
+ |
+ |
+ |
+++ |
Multi2 |
Multi-purpose greases |
Multi3 |
|
–30 |
+120 |
+75 |
Lithium soap |
Mineral oil |
Multi3 |
3 |
80 |
++ |
+ |
+ |
+ |
++ |
++ |
++ |
Multi3 |
Grease |
Characteristic applications |
Operating temperature |
Continuous limit |
Thickener |
Base oil |
Grease |
Consistency |
Base oil viscosity at +40 °C |
Temperatures |
Low friction, high speed |
High load, low speed |
Vibrations |
Support for seals |
Relubrication facility |
Grease |
|||
°C |
°C |
NLGI |
mm2/s |
|||||||||||||||
from |
to |
Low |
High |
|||||||||||||||
High loads |
Load150 |
|
–20 |
+140 |
+95 |
Lithium complex soap |
Mineral oil |
Load150 |
2 |
160 |
+ |
++ |
– |
+++ |
++ |
++ |
++ |
Load150 |
High loads |
Load220 |
|
–20 |
+140 |
+80 |
Lithium/calcium soap |
Mineral oil |
Load220 |
2 |
245 |
+ |
+ |
– |
+++ |
++ |
++ |
++ |
Load220 |
High loads |
Load400 |
|
–401) |
+130 |
+80 |
Lithium/calcium soap |
Mineral oil |
Load400 |
2 |
400 |
+ |
+ |
– |
+++ |
++ |
++ |
++ |
Load400 |
High loads |
Load460 |
|
–401) |
+130 |
+80 |
Lithium/calcium soap |
Mineral oil |
Load460 |
1 |
400 |
++ |
+ |
– |
+++ |
++ |
– |
++ |
Load460 |
High loads |
Load1000 |
|
–301) |
+130 |
+80 |
Lithium/calcium soap |
Mineral oil |
Load1000 |
2 |
1 000 |
+ |
+ |
–– |
+++ |
++ |
++ |
++ |
Load1000 |
Grease |
Characteristic applications |
Operating temperature |
Continuous limit |
Thickener |
Base oil |
Grease |
Consistency |
Base oil viscosity at +40 °C |
Temperatures |
Low friction, high speed |
High load, low speed |
Vibrations |
Support for seals |
Relubrication facility |
Grease |
|||
°C |
°C |
NLGI |
mm2/s |
|||||||||||||||
from |
to |
Low |
High |
|||||||||||||||
High temperatures |
Temp90 |
|
–40 |
+160 |
+90 |
Polycarbamide |
Partially synthetic oil |
Temp90 |
3 |
148 |
+++ |
++ |
+ |
+ |
+ |
++ |
++ |
Temp90 |
High temperatures |
Temp110 |
|
–35 |
+160 |
+110 |
Lithium complex soap |
Partially synthetic oil |
Temp110 |
2 |
130 |
+++ |
+++ |
++ |
+ |
+ |
+ |
+ |
Temp110 |
High temperatures |
Temp120 |
|
–30 |
+180 |
+120 |
Polycarbamide |
Alkoxyfluoro oil |
Temp120 |
2 |
400 |
++ |
+++ |
– |
+++ |
+ |
++ |
+ |
Temp120 |
High temperatures |
Temp200 |
|
–30 |
+260 |
+200 |
PTFE |
Fluoridated polyether oil |
Temp200 |
2 |
550 |
++ |
+++ |
–– |
++ |
+ |
+ |
+ |
Temp200 |
Special requirements |
Speed2.6 |
|
–40 |
+120 |
+80 |
Lithium complex soap |
Synthetic oil |
Speed2.6 |
2 – 3 |
25 |
+++ |
+ |
+++ |
–– |
– |
+ |
+ |
Speed2.6 |
Special requirements |
Vib3 |
|
–30 |
+150 |
+90 |
Lithium complex soap |
Mineral oil |
Vib3 |
3 |
170 |
++ |
++ |
– |
++ |
+++ |
++ |
– |
Vib3 |
Special requirements |
FOOD2 |
|
–30 |
+120 |
+70 |
Aluminium complex soap |
Synthetic oil |
FOOD2 |
2 |
150 |
++ |
– |
+ |
+ |
+ |
+ |
+++ |
FOOD2 |
Special requirements |
CLEAN M |
|
–30 |
+180 |
+90 |
Polycarbamide |
Ester |
CLEAN M |
2 |
103 |
+++ |
+++ |
+ |
+ |
+ |
+ |
++ |
CLEAN M |
Special requirements |
Motion2 |
|
–40 |
+130 |
+75 |
Lithium soap |
Synthetic oil |
Motion2 |
2 |
50 |
+++ |
+ |
– |
++ |
+++ |
++ |
+ |
Motion2 |
Grease |
Characteristic applications |
Operating temperature |
Continuous limit |
Thickener |
Base oil |
Grease |
Consistency |
Base oil viscosity at +40 °C |
Temperatures |
Low friction, high speed |
High load, low speed |
Vibrations |
Support for seals |
Relubrication facility |
Grease |
|||
°C |
°C |
NLGI |
mm2/s |
|||||||||||||||
from |
to |
Low |
High |
- Measurement values according to Schaeffler FE8 low temperature test.
Available containers
Grease container sizes
Arcanol grease1) |
Tube |
Cartridge |
Can |
Bucket |
Hobbock |
Drum |
|||
---|---|---|---|---|---|---|---|---|---|
70 g |
250 g |
400 g |
1 kg |
5 kg |
12,5 kg |
25 kg |
50 kg |
180 kg |
|
Multitop |
‒ |
● |
● |
● |
● |
● |
● |
‒ |
● |
Multi2 |
‒ |
● |
● |
● |
● |
● |
● |
‒ |
● |
Multi2 |
‒ |
● |
● |
● |
● |
● |
‒ |
‒ |
● |
Load150 |
‒ |
‒ |
● |
● |
‒ |
● |
‒ |
● |
‒ |
Load220 |
‒ |
‒ |
● |
● |
‒ |
● |
● |
‒ |
● |
Load400 |
‒ |
‒ |
● |
● |
● |
● |
● |
● |
● |
Load460 |
‒ |
‒ |
● |
● |
● |
● |
‒ |
● |
● |
Load1000 |
‒ |
‒ |
‒ |
‒ |
● |
‒ |
● |
● |
● |
Temp90 |
‒ |
‒ |
● |
● |
● |
‒ |
● |
‒ |
● |
Temp110 |
‒ |
‒ |
● |
● |
‒ |
‒ |
‒ |
● |
‒ |
Temp120 |
‒ |
‒ |
● |
● |
● |
‒ |
● |
‒ |
‒ |
Temp200 |
● |
‒ |
‒ |
● |
‒ |
‒ |
‒ |
‒ |
‒ |
Speed2.6 |
‒ |
● |
● |
● |
‒ |
‒ |
● |
‒ |
‒ |
Vib3 |
‒ |
‒ |
● |
● |
● |
‒ |
● |
● |
‒ |
FOOD2 |
‒ |
‒ |
● |
● |
‒ |
● |
● |
‒ |
‒ |
CLEAN M |
‒ |
● |
● |
● |
‒ |
‒ |
‒ |
‒ |
‒ |
Motion2 |
‒ |
● |
● |
● |
● |
● |
● |
● |
‒ |
- Other containers are available by agreement.