Mounting and dismounting
General guidelines
In the interests of the user, the applicable legal regulations and other directives relating to environmental protection and occupational safety must be observed.
ACHTUNG
Plain bearings must be handled with care before and during mounting. Problem-free functioning of the sliding surfaces is substantially dependent on the care taken in mounting. The sliding surfaces must not be damaged. It must be ensured that mounting is carried out in clean conditions.
The bearings will only achieve their maximum operating life and functional capability if they are mounted correctly. Where a mounting position is specified, this must be observed in all cases.
Further information
Schaeffler offers products and services for the mounting and dismounting of plain bearings..
Delivered condition
The plain bearings are supplied with preservative in a box, or in a bag held in a box or in a crate. Depending on their design, rod ends are supplied protected by a preservative or with a zinc coating.
ACHTUNG
Any change, irrespective of the bearing type, will reduce their operating life.
Bearings must not be treated or cleaned using trichloroethylene, perchloroethylene, petroleum spirit or other solvents.
Substances containing oil will change the characteristics of the bearings.
Storage of bearings
Plain bearings should be stored:
- in the original packaging
- in clean, dry areas
- at as constant a temperature as possible
- at a relative humidity of max. 65%.
Unpacking of bearings
Plain bearings should only be removed from their packaging immediately before mounting:
- Hands should be kept clean and dry and protective gloves worn if necessary (perspiration leads to corrosion).
- If the original packaging is damaged, the products must be checked.
- If the products are contaminated, they must be wiped with a clean cloth only.
Guidelines for mounting
The guidelines for mounting must be followed precisely and the operating specifications must be observed:
- If not, there is a direct or indirect hazard to personnel, the product or the adjacent construction.
- The bearings must be protected against moisture and aggressive media.
- The bearings must always be located concentrically.
- Mounting may only be carried out by qualified personnel. If errors are made in mounting, no claims may be made under warranty. Schaeffler assumes no liability for damage caused by defective mounting, incorrect maintenance, incorrect communication of the content of this chapter to third parties or a failure to communicate the content.
Maintenance-free plain bearings
ACHTUNG
Plain bearings with maintenance-free sliding layers must not be lubricated. The use of lubricant will lead to a considerable reduction in the operating life.
Maintenance-free spherical plain bearings and maintenance-free plain bushes should be mounted such that no lubricant or other substances used to aid mounting can reach the sliding surfaces.
Transport of large radial spherical plain bearings
Large spherical plain bearings must only be transported using the eye bolts supplied. For this purpose, the radial bearings have threaded holes on the end faces of the inner and outer rings, ➤ Figure.
Transport by means of eye bolts
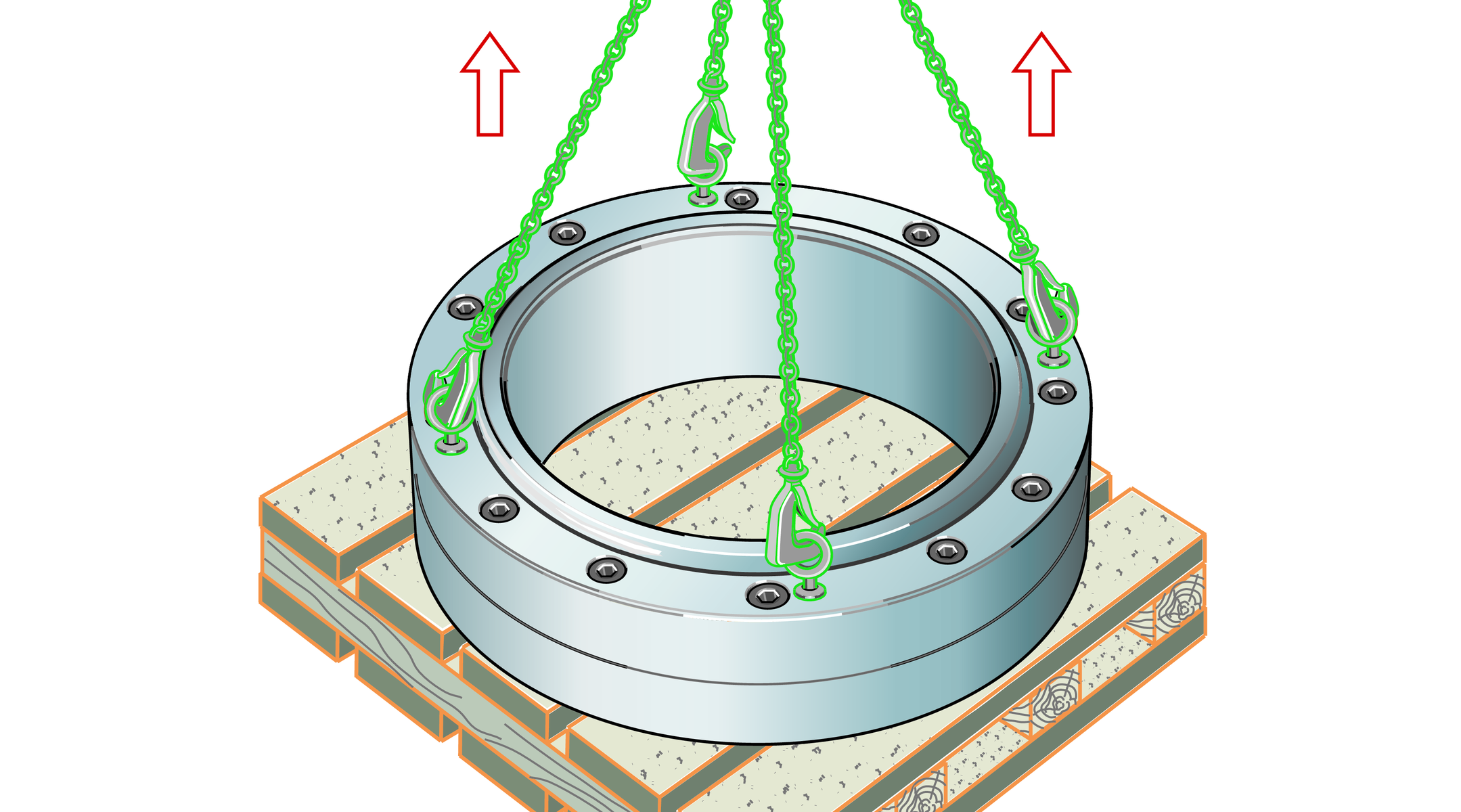
Orientation for mounting of large radial spherical plain bearings
For the mounting of large radial spherical plain bearings GE..-DW and GE..-DW-2RS2, it must be ensured that the screw connection on one side of the outer ring halves is facing towards the open side of the bearing. This makes subsequent dismounting easier.
Checking the adjacent construction
Before mounting of spherical plain bearings, rod ends and plain bushes, the adjacent construction must be checked as follows:
- the quality of the bearing seating surface on the shaft and housing bore
- the dimensional and geometrical accuracy of seating and locating faces
- the shaft and housing seats
- any chamfers, radii and edge breaks required on the shaft and housing bore.
Any burrs present must be removed.
If tight fits are present or mounting conditions present difficulties, the surface of the shaft and housing bore should be lightly oiled.
ACHTUNG
If welding work is carried out on the adjacent construction, welding currents must not be allowed to pass through the spherical plain bearing, since this will immediately damage the sliding surfaces.
Positioning of the joint
In radial spherical plain bearings with outer rings split at one and two points, the joints must be positioned at 90° to the main load direction, ➤ Figure.
The lubrication holes in bearings requiring maintenance are thus positioned directly in the load zone. This allows good lubricant distribution in the load zone area.
Position of joint in main load direction
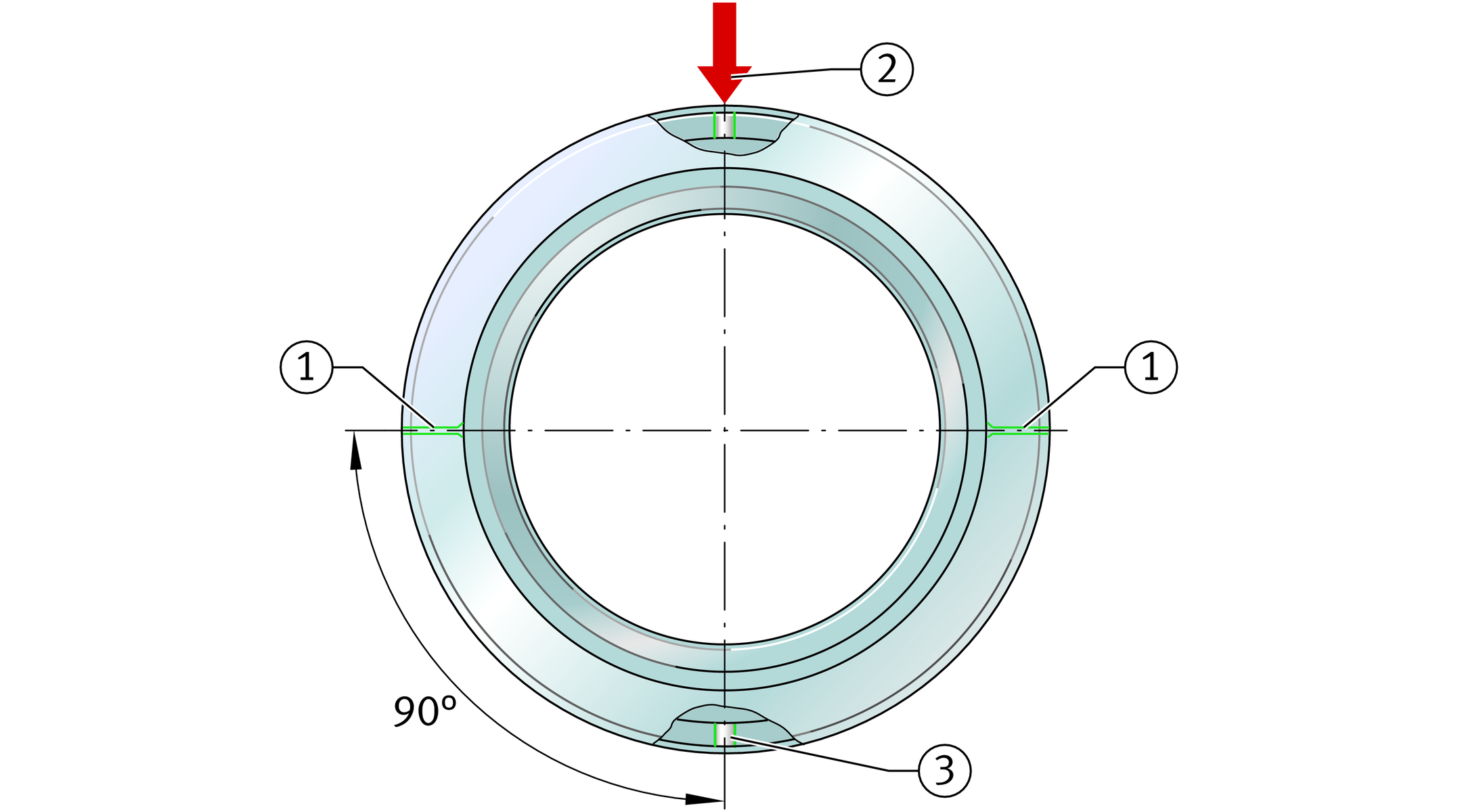



Adhesive bonding of bearing rings
If the recommended fits are observed, adhesive bonding of the bearing rings is not generally necessary.
Adhesives may only be used on spherical plain bearings with steel/steel sliding contact surfaces under the following conditions:
- The surfaces to be bonded must be clean and free from grease.
- The raceways must be cleaned using a cleaning agent and well lubricated using a paste with a high MoS2 content.
- It must be ensured that the lubricant ducts and lubricant holes are not blocked by adhesive.
Pressing in of spherical plain bearings
Always apply mounting forces to the bearing ring to be mounted, ➤ Figure. If these forces are directed through the sliding surfaces, this could lead to jamming of the bearings during mounting.
When mounting the bearings on a shaft and in a housing, the mounting tools used must act simultaneously on the end faces of the inner and outer ring, ➤ Figure.
Larger bearings must be mounted using special mounting equipment, ➤ Figure. As the bearing diameter increases, so do the mounting forces required and simple impact type tools are no longer adequate in these cases.
Further information on the mounting and maintenance of plain bearings is available from the industrial service function of Schaeffler.
ACHTUNG
Avoid direct blows with a hammer and drift on the end faces of the bearing rings, since this can lead to microcracks in the bearing.
Mounting forces and bearing ring to be mounted
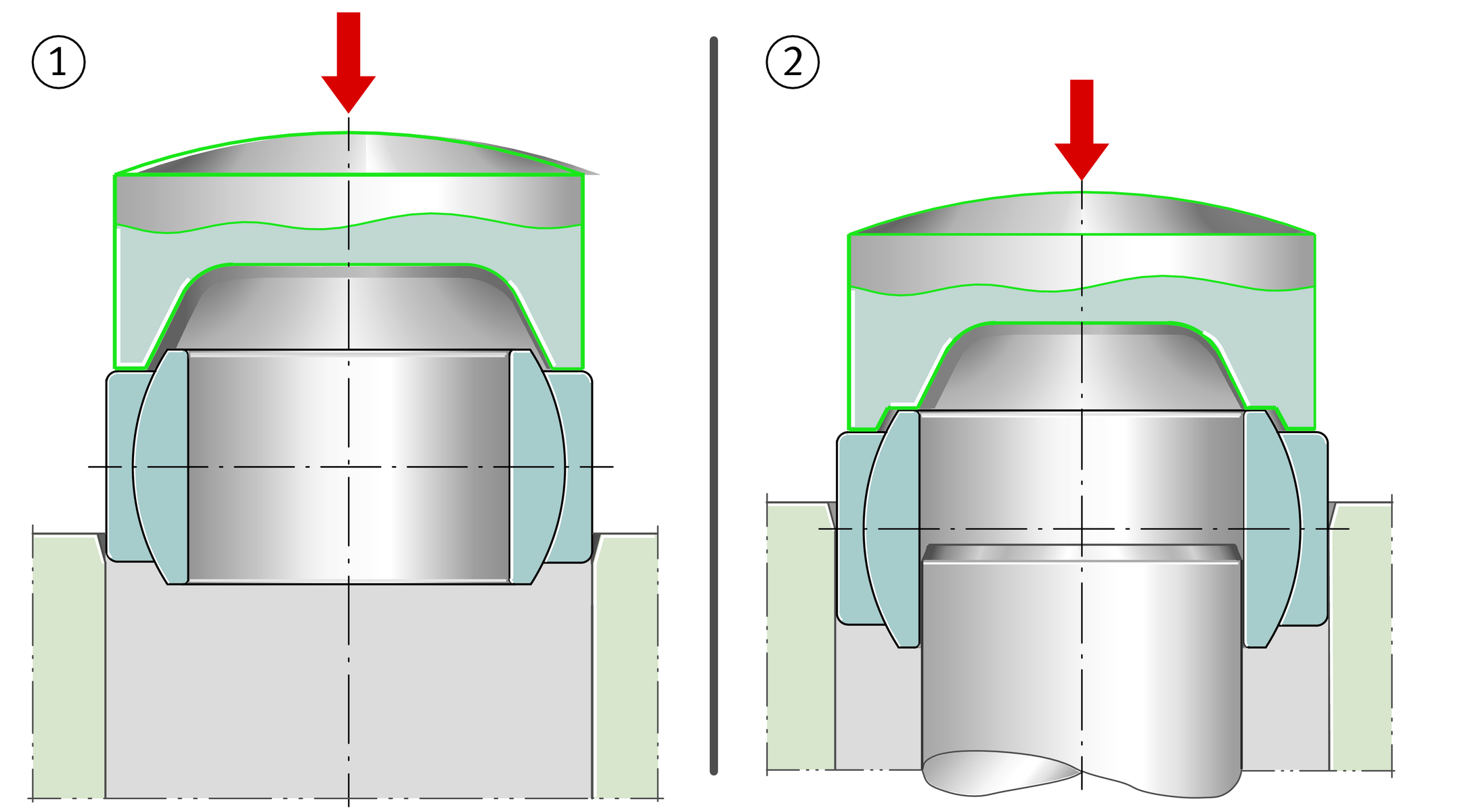


Special mounting equipment for larger bearings
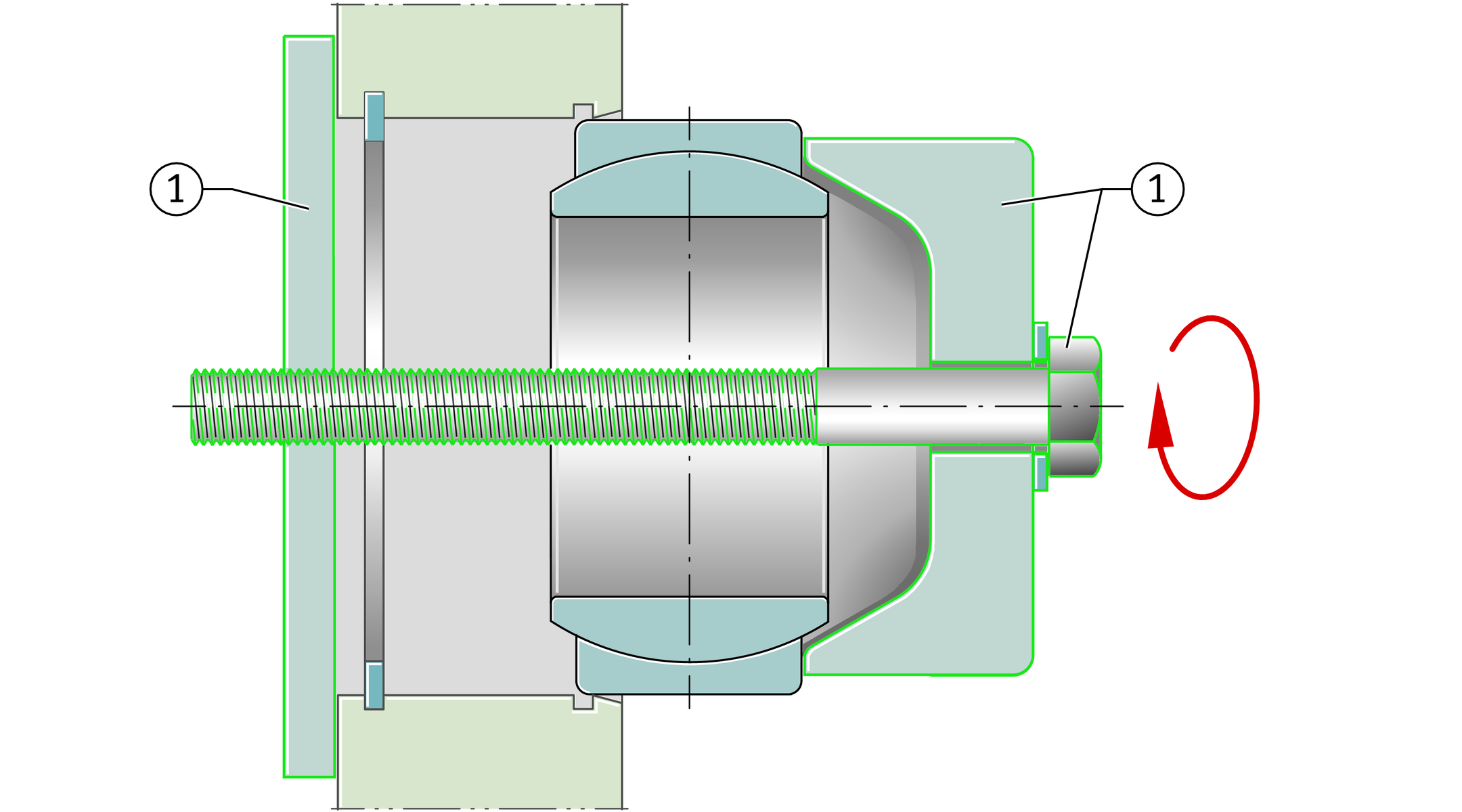

Hydraulic assistance
For special spherical plain bearings with a conical bore, hydraulic nuts are used in conjunction with hydraulic pumps.
Pressing in of bushes
The bushes can be easily pressed into the housing bore. The bushes can be pressed in more easily if the bush backing or housing bore is lightly oiled.
Bushes can be pressed in flush or into a counterbore using a press-in mandrel, ➤ Figure and ➤ Figure. In the case of metal/polymer composite plain bushes, an auxiliary ring should additionally be used due to the butt joint for a diameter equal to or greater than ≧ 55 mm, ➤ Figure.
The chamfer on the mandrel must have rounded transitions or rounding of the end.
ACHTUNG
Sharp transitions on the entry side of the shaft and mandrel will damage the sliding layer during mounting and reduce the operating life of the plain bearings.
Diameter of press-in mandrel
Series | Press-in mandrel | |||
---|---|---|---|---|
Outside diameter dD1 | Shoulder diameter dD2 | |||
Metal/polymer composite plain bushes | Di | –0,1–0,2 | Do | –0,2–0,3 |
ELGOTEX filament wound bushes | Di | –0,3–0,5 | ||
ELGOGLIDE plain bushes |
Pressing bush in flush
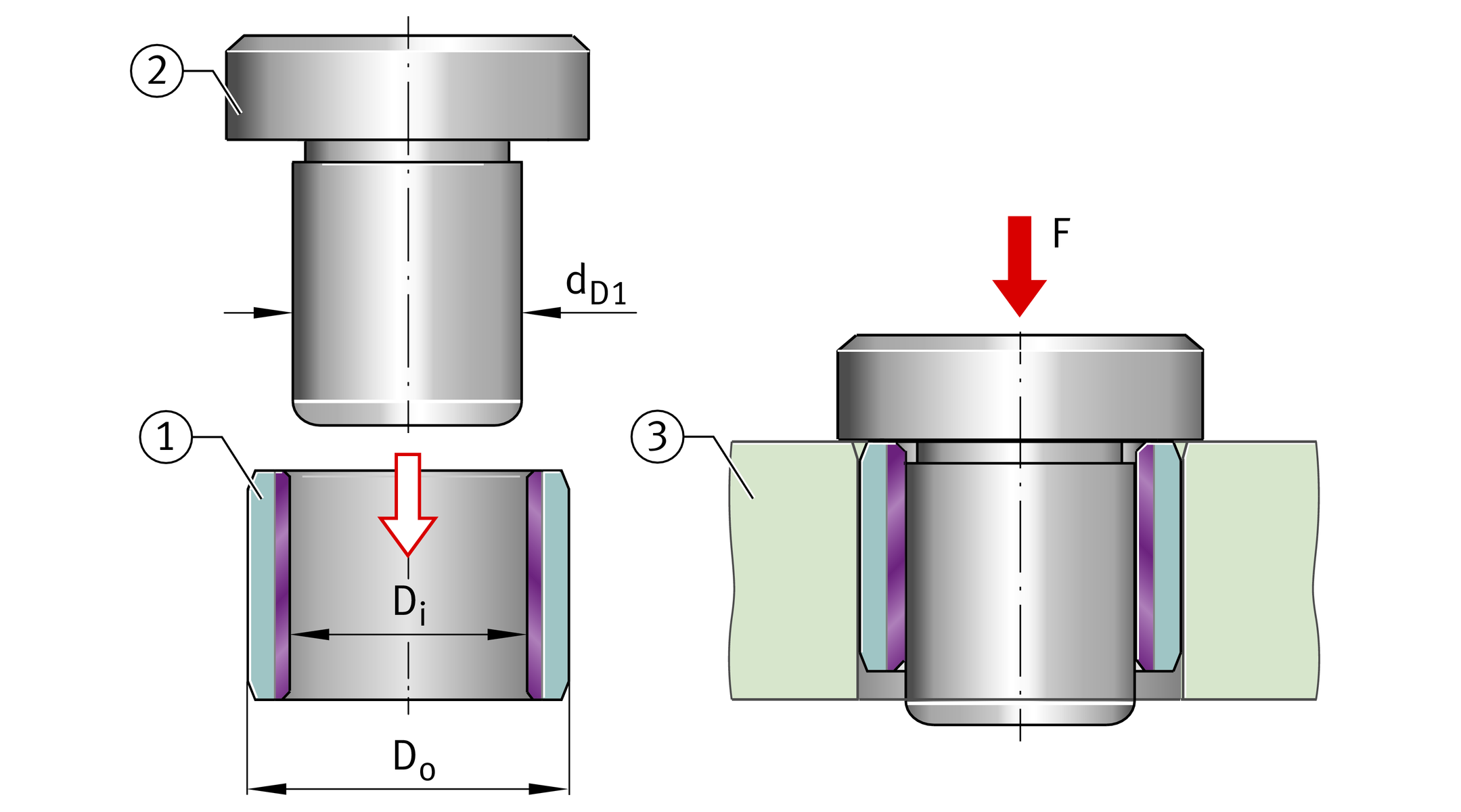



Pressing bush into a counterbore
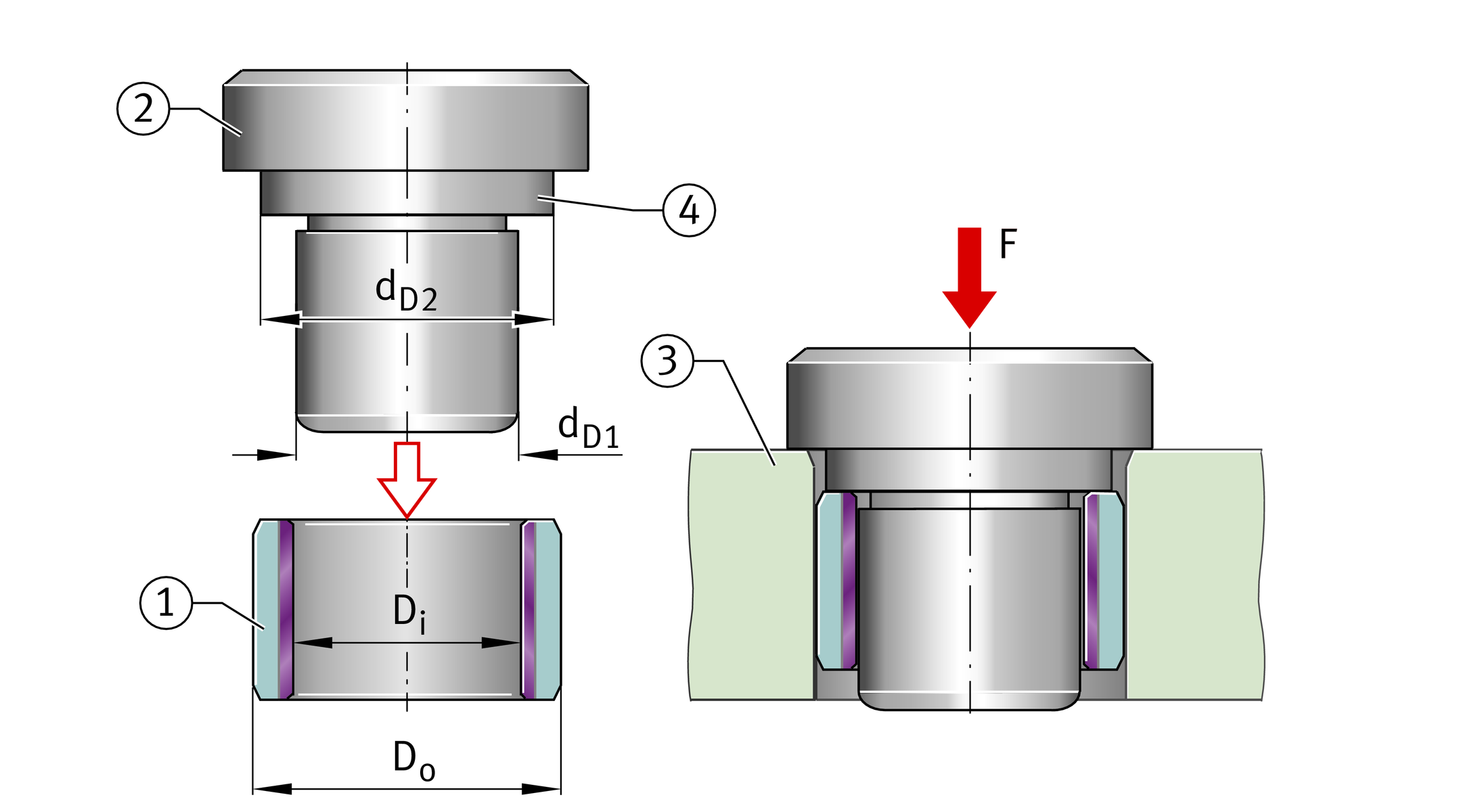




Auxiliary ring for metal/polymer composite plain bushes with Do ≧ 55 mm
Outside diameter of bush Do | Inside diameter of auxiliary ring dH | |
---|---|---|
mm | mm | |
55 ≦ Do ≦ 100 | Do | +0,28+0,25 |
100 < Do ≦ 200 | Do | +0,4+0,36 |
200 < Do ≦ 305 | Do | +0,5+0,46 |
Pressing bush in using auxiliary ring
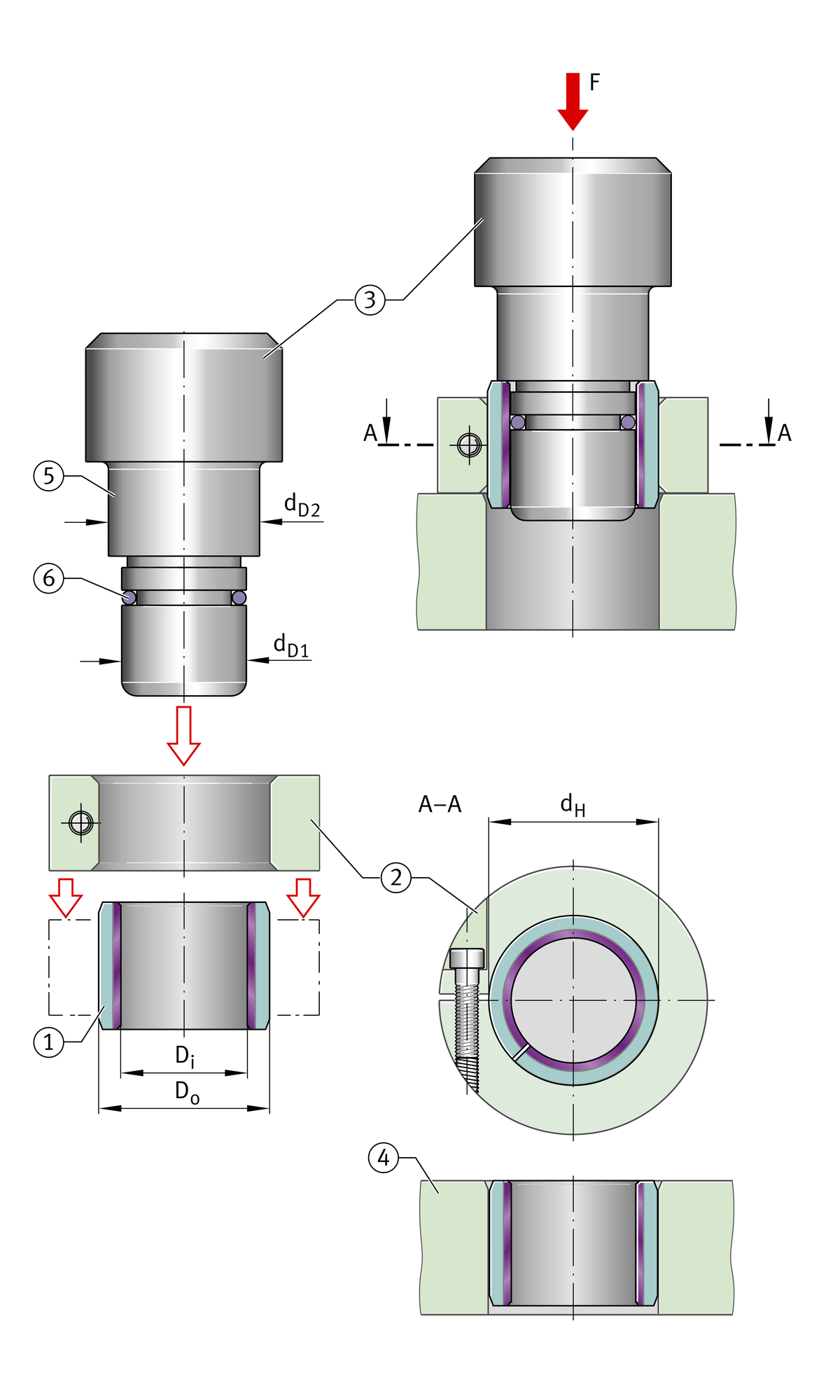






Thermal assistance
In order to reduce the mounting forces, spherical plain bearings can be heated.
ACHTUNG
Do not heat bearings to more than +130 °C, since higher temperatures will damage the seals in sealed bearings.
Spherical plain bearings must not be heated in an oil bath:
- In the case of maintenance-free spherical plain bearings, this affects the tribological system.
- In the case of spherical plain bearings requiring maintenance with a steel/steel sliding contact surface, this will change the concentration of molybdenum disulphide on the sliding surfaces.
Bearings must not be heated using a naked flame:
- The material undergoes excessive localised heating, reducing its hardness.
- Furthermore, stresses are induced in the bearing.
- The seals could melt.
- Maintenance-free sliding layers could be damaged.
Mounting by means of refrigeration
The structure of the rings of radial spherical plain bearings with a steel/steel sliding contact surface will change at temperatures below –61 °C. Due to the structural change, their volume may increase; the change to the tolerances may lead to jamming of the bearing.
If this mounting method is to be used, the bearing rings can be supplied with appropriate heat treatment. Please consult the Schaeffler engineering service.
For easier fitting, maintenance-free ELGOGLIDE plain bushes can be cooled for a short time in liquid nitrogen at –196 °C.
ACHTUNG
When mounting by means of refrigeration, it must be ensured that the operating temperature of the respective seal is not lower than the specified value, otherwise the seal may be destroyed.
RS seals can be easily dismantled before assembly, TS seals cannot be dismantled.
It must be ensured that the seals are later reassembled correctly and in the correct position.
In the case of plain bushes with integrated seals 2RS, the correct seating of the seals in the undercut must be checked after refrigeration.
Tools for thermally assisted mounting
Heating can be carried out using heating cabinets with a controllable thermostat, induction heating devices, ➤ Figure, or medium frequency technology. The advantages include uniform heating, no contamination of components and the absence of long preheating times.
Further information is available from the industrial service function of Schaeffler.
ACHTUNG
Localised heating must be avoided. The bearing temperature must be monitored using a thermometer.
Information in the catalogue and manufacturer's data on grease and seals must be observed.
Heating by means of an induction heating device
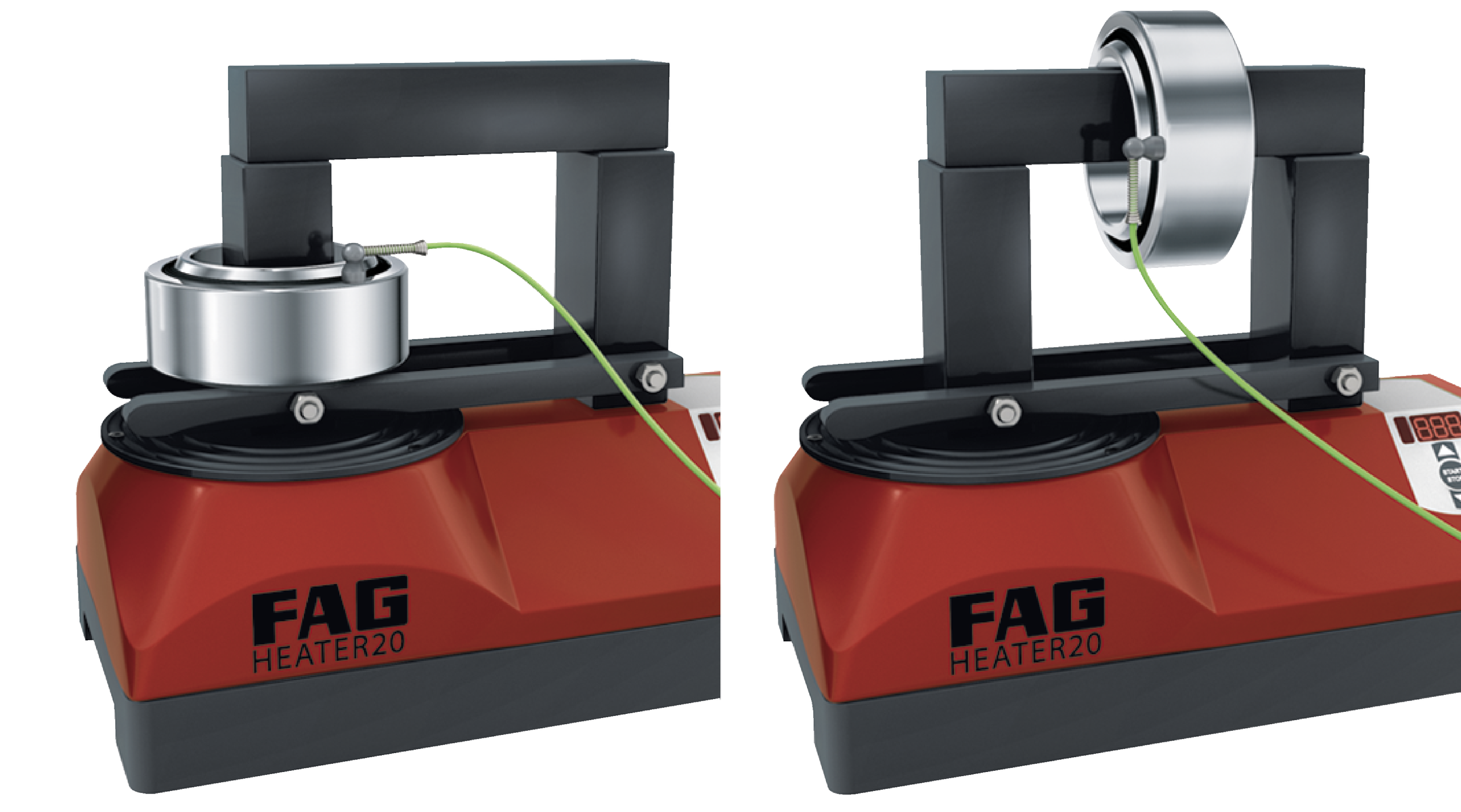
Dismounting of spherical plain bearings
Even if the force is applied to the ring to be dismounted in accordance with the specification in the case of spherical plain bearings, the frictional contact of the other ring due to the fit presents difficulties in dismounting.
Depending on the joint pressure, contraction of the inner ring and expansion of the outer ring will occur, ➤ Figure. The extraction forces also increase with increasing joint pressure.
Contraction of the inner ring and expansion of the outer ring
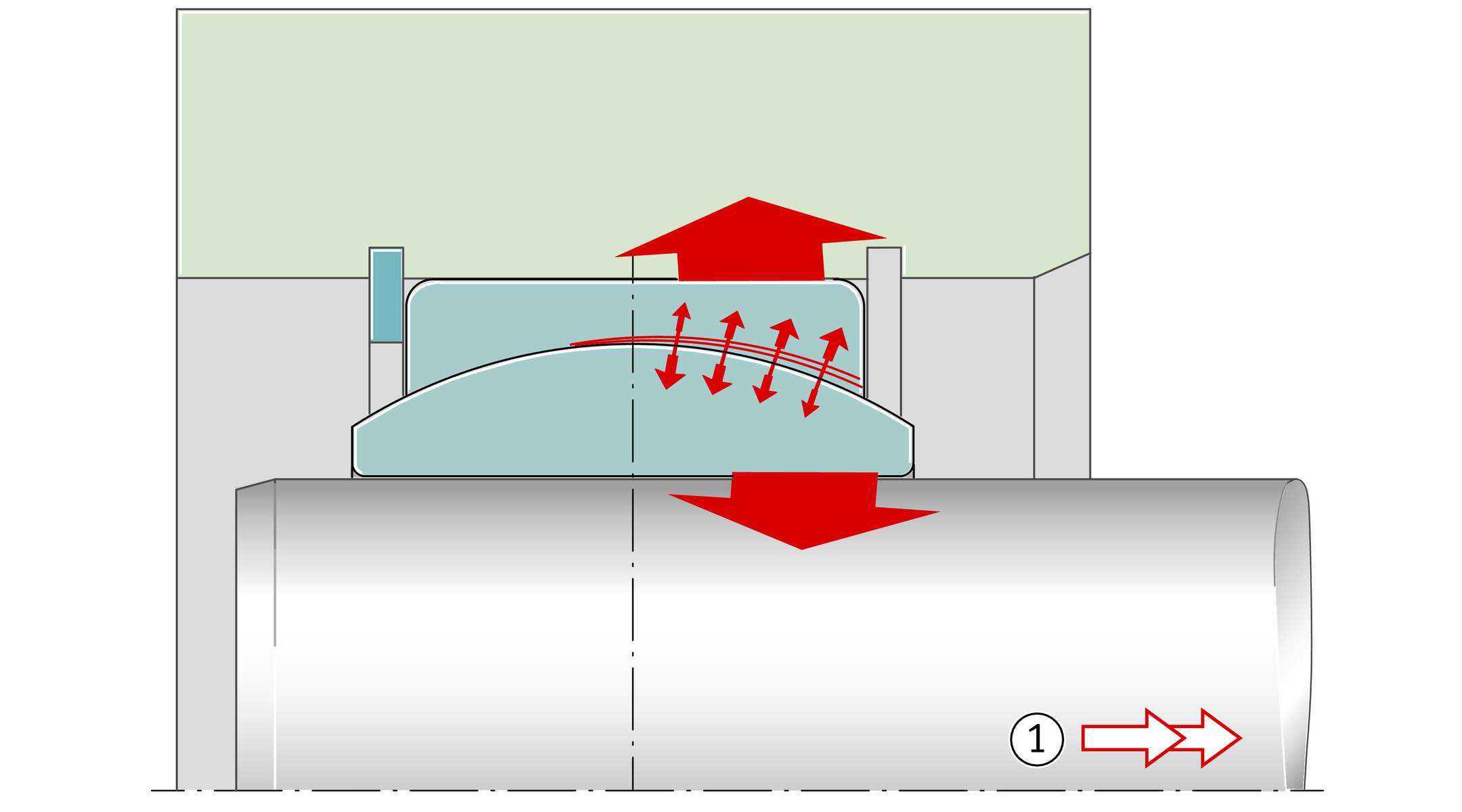

Precautions for dismounting
Dismounting of spherical plain bearings can be facilitated if the following design precautions are taken:
- a threaded hole for an extraction screw in the shaft, ➤ Figure
- threaded holes for extraction screws in the housing, ➤ Figure
- milled areas on the stud for the jaws of the extraction device, ➤ Figure.
Threaded hole in the shaft
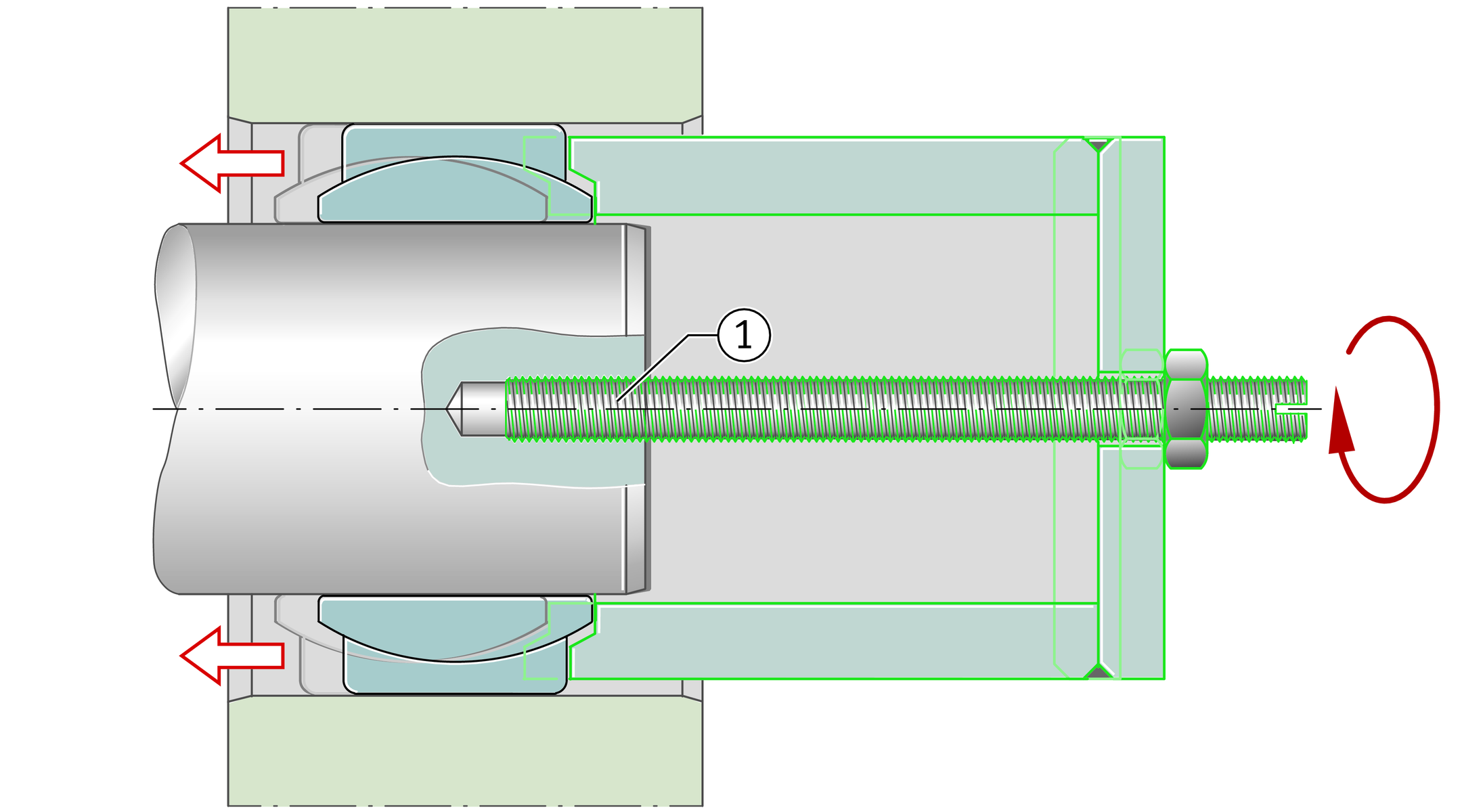

Threaded hole in the housing and milled areas for extractors
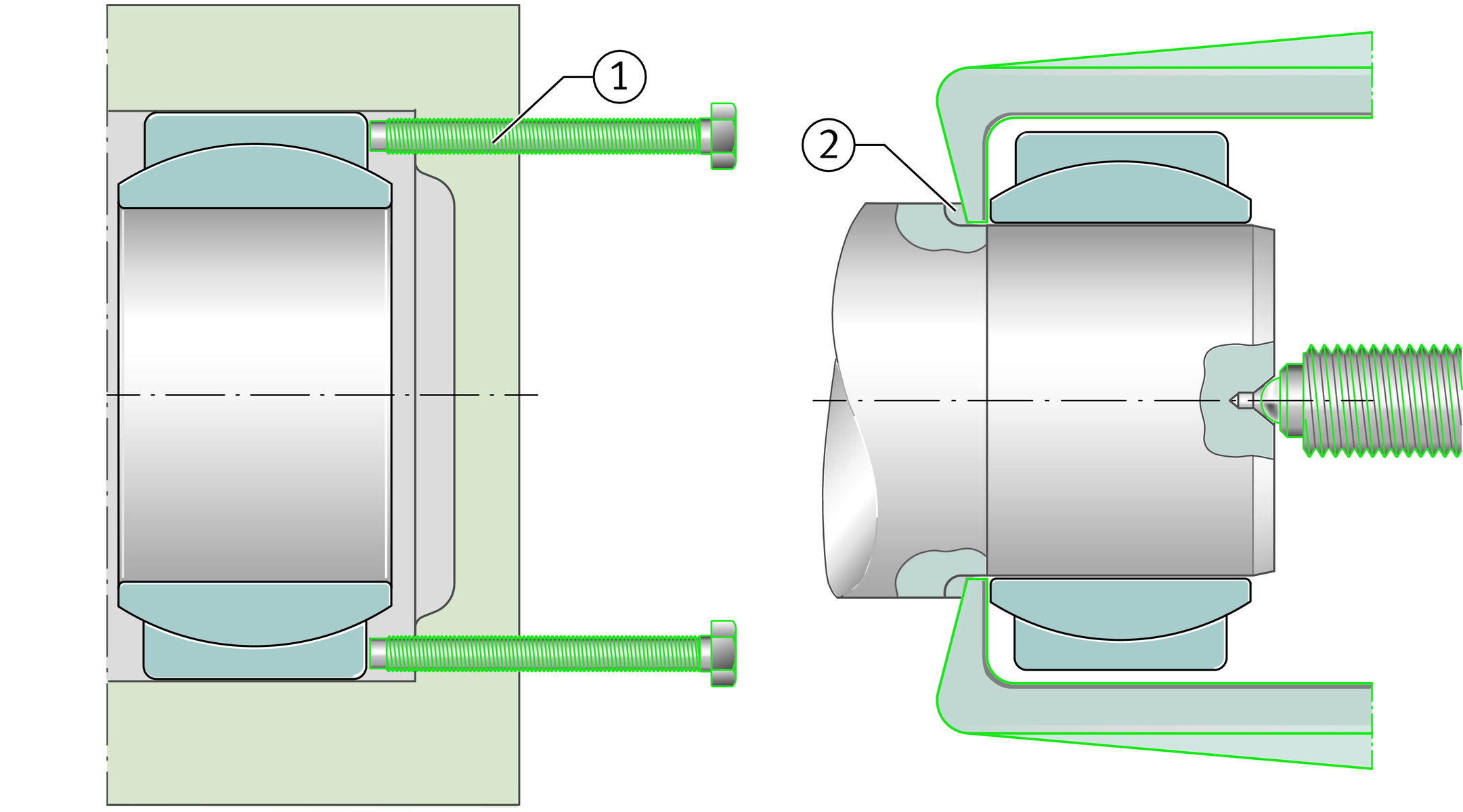

