Customer Success Story
Ensure Transparency – Increase Energy Efficiency
The first step in becoming energy efficient is to identify energy sources and peaks. At the Schaeffler site in Höchstadt, Germany, the “investigations” have been in full swing for years. The goal was and is to use the gained insights to develop suitable measures that contribute to increasing energy efficiency. To create transparency here, the maintenance team was already using energy measurement systems. However, these did not fully meet expectations and there were still enough blind spots. Therefore, the maintenance team decided to use the Power-Adapt energy monitoring system, which has recently been added to the Schaeffler portfolio. This solution can handle up to six measuring points. The cost-effective Power-Adapt energy monitoring solutionis based on ISO 50001; it measures precisely and is very easy to install.
Conclusion: Thanks to the precise measurements, of the retrofit Power-Adapt energy monitoring solution, it was able easy to identify blind spots and derive appropriate measures.
Challenge
Any kilowatt hour saved is very welcome ...
At this location, approximately 1,500 Schaeffler employees work in office buildings, shop floors or centers 5 days a week. Light is needed in all buildings, electricity is needed to operate the machines, the refrigerator must keep food and beverages fresh, and the ventilation systems must function. The list could be continued endlessly. The common denominator: All machines, aggregates and elements require energy, some more, some less. Höchstadt receives the electricity bill every month. It shows the total consumption in kilowatt hours (kWh), but what cannot be seen is how much electricity a single unit or machine consumes. In order to get closer to a climate-neutral production, around 100 gigawatt hours are to be saved by 2030. That is a considerable amount of energy. 100 GWh would be enough to supply more than 25,000 households with electricity for one year, or to power an electric vehicle for more than 500 million kilometers.
Little by little, the bird builds its nest ...
Without an energy monitoring system, it is difficult to determine power consumption precisely. For example, for light sources, the power consumption in watts would have to be known, and for machines, the power consumption in kilowatt hours. Then that would have to be multiplied by the time during which the systems are operated to determine the energy consumption. This is too imprecise, because if, for example, a machine is not running smoothly or the light is flickering, this can lead to increased power consumption. That is why Schaeffler Höchstadt has been using energy monitoring systems in buildings and plants for years to gain precise insights into power consumption. These have helped to increase energy efficiency, but not significantly enough.
Like detectives on the trail ...
“Our work resembles that of a detective. In our case, the crime scene is our Höchststadt site with its different power consumption levels in the plants and buildings. The suspects are the energy peaks. We have to find them, along with the blind spots. Only with these insights can we develop suitable measures to increase energy efficiency. Due to the large number of energy consumers, we need a cost-effective and easy-to-integrate solution that provides us with detailed information about energy consumption. The systems we have used so far have not been able to do this to the full extent,” says Michael Sommer, Bearings & Industrial Solutions Specialist for Digitalization & Maintenance in the Europe region.
To learn more about the customer, download the PDF of the Customer Success Story here.
Solution
What characterizes the solution?
Six times three current phases to be recorded The ability to connect six times three current phases (Alternating current) in an energy measurement system allowed maintenance to measure the machines and production lines in the buildings and plants separately. This provided detailed insights into energy consumption and into areas with the highest optimization potential. This made it possible to collect detailed data on energy consumption and performance. Both active and reactive power measurements were taken by the system.
Easy to use and integrate – zero-error principle “No drilling and no screws were needed to to install the solution – that impressed me a lot,” says Michael Sommer. Power-Adapt could be integrated into the existing IT infrastructure via Modbus just as easily. All that was needed was to enter the IP and Mac address, along with a little data, into the existing Schaeffler software. Installation errors are virtually eliminated because the power monitoring system would automatically detects those. In addition, the installation is validated during the configuration process, during which physical errors can also be compensated for.
Precise measurements, good performance
The following examples show how precise the measurements are:
Example 1: Thanks to Power-Adapt, it was discovered that a ventilation system consumes almost as much electricity as the heavy presses in the plant. The other two systems did not recognize this blind spot. “We would never have thought that a ventilation system consumes so much power, and we are now glad that we have identified this blind spot. With this knowledge, and after a more in-depth analysis, we will take measures to stop this enormous energy consumption,” says the maintenance specialist Michael Sommer.
Example 2: To compare the already established energy monitoring systems with Power-Adapt, a vertical grinder and a conditioning system were monitored with Power-Adapt. These machines are located in different buildings. To measure the currents of the phases, current measuring clamps were used, just as in example 1. After the energy monitoring system was installed in the control cabinet and connected to the machines, wireless communication was established with the gateway via LoRaWAN. Via the gateway, the data reached the Power-Cloud via LTE connectivity. Once the data was visible, it was possible to see that Power-Adapt, compared to the other devices, measures very precisely, sometimes even more accurately (Figure 1). The energy monitoring system also measures forward and reverse power separately.
Reasonable initial costs, few surprises
Compared to other power monitoring systems, Power-Adapt stands out due to its unique price-performance ratio. It was therefore not difficult for Schaeffler Höchstadt to decide to use the power monitoring system in every plant and building in the future. One plus: By automatically generating alarms, Power-Adapt can maximize operational efficiency, reduce costs and ensure the reliability and safety of energy systems.
More transparency, automated documentation
With Power-Adapt, the team receives comprehensive documentation. This includes analyses and reports such as historical data or comparative analyses, cost, alarm and CO2 emission reports. The automatically generated energy efficiency reports are accessible via a cloud platform and allow for location-independent access. This comprehensive documentation helps the maintenance team to identify measures that contribute to increased efficiency and cost reduction and to promote climate-neutral production.
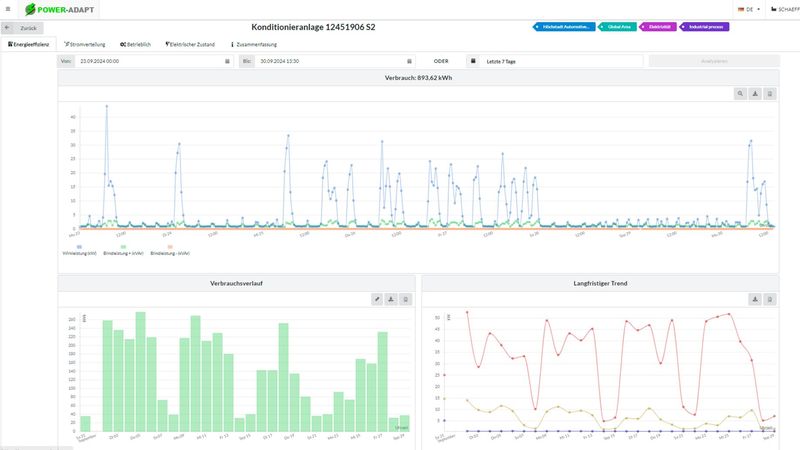
One of many views
In the Power-Cloud, maintenance staff can view the data in their personalized web-based user interface and display various diagrams. Whether as a pie chart, bar chart or curve diagram – the dashboard offers many options for visualizing, comparing and analyzing the data.
The figure shows the total consumption, consumption history and a trend of the conditioning system over the period of one week. The time period for the data display can be set individually. Similarly, data from multiple machines can be displayed, compared and analyzed.
Technical Information
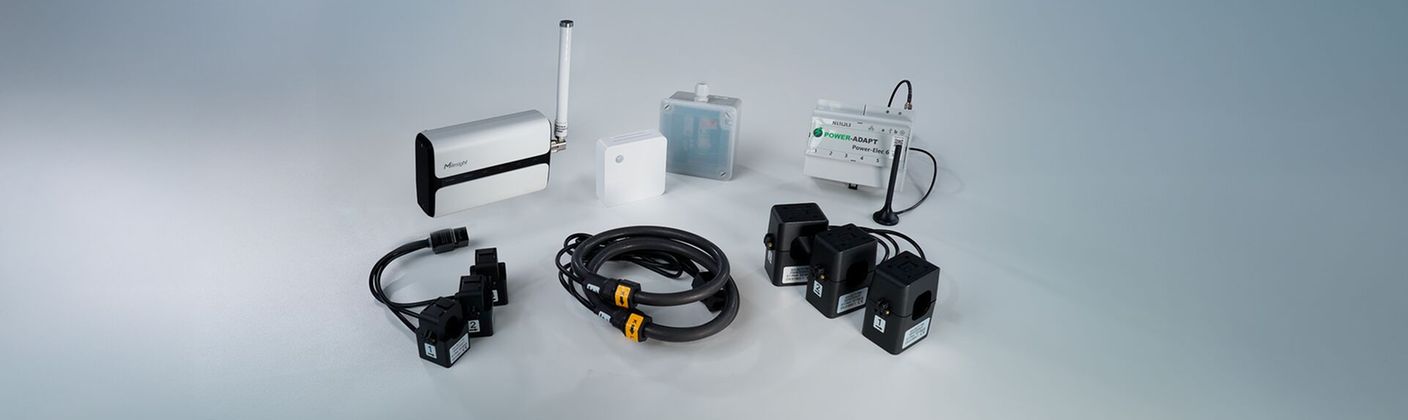
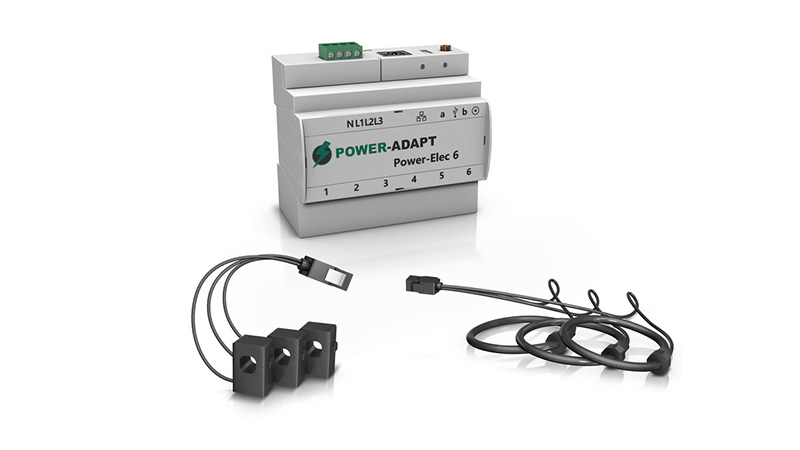
Electric energy metering
Power-Elec electricity meters with multiple connections for monitoring in control cabinets. Split current trans- former sets and flexible Rogowski coils enable current measurement of electric current intensity.
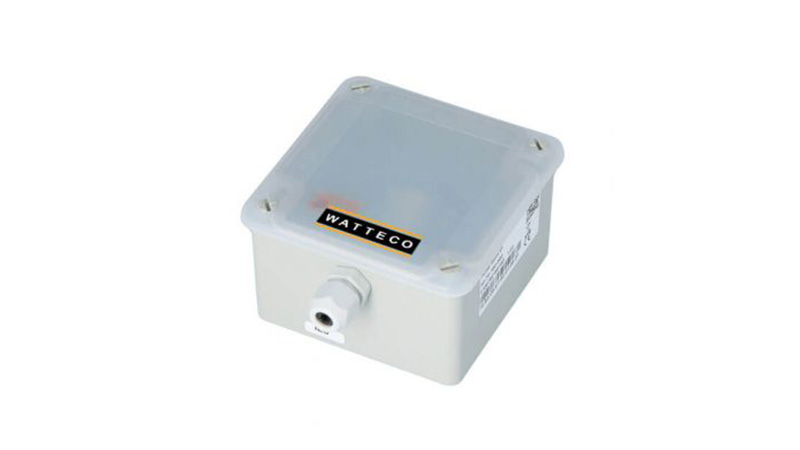
Reading existing meters
Power-Pulse integrates your existing electricity or fluids meters (gas, etc.) into our cloud platform, allowing you to go beyond electricity metering.
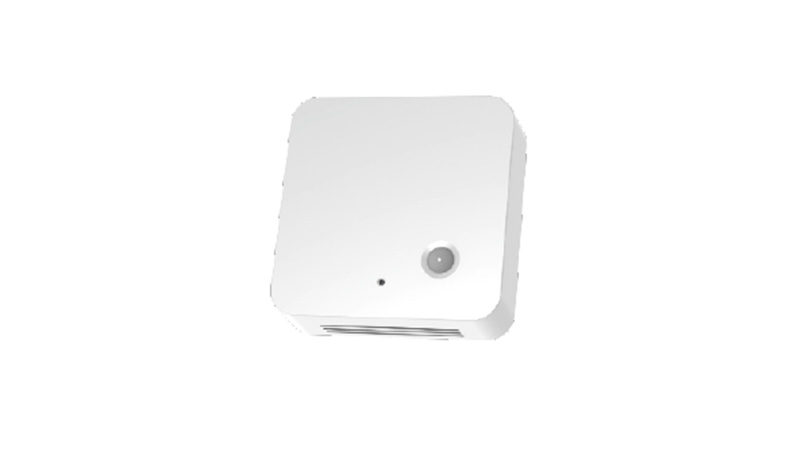
Measuring ambiant variables
Ambient sensors measure and report temperature, humidity, pressure, CO₂ or fine particle levels in your installations.
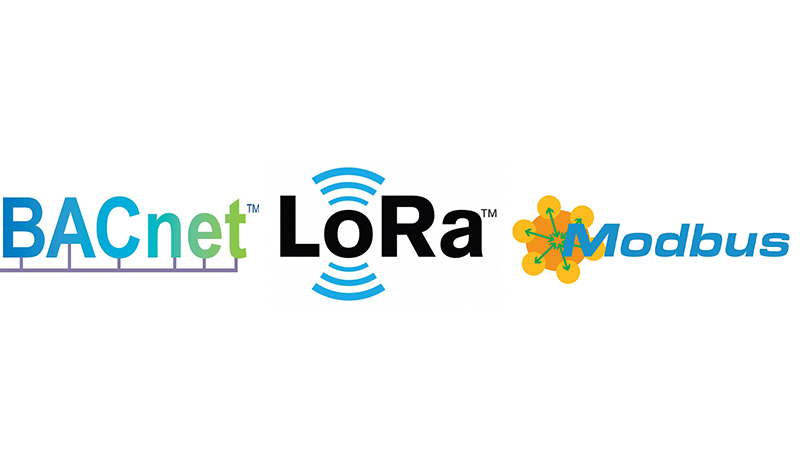
Wired or wireless connectivity
Power-Elec incorporates standard wired protocols such as BACnet and Modbus TCP and RTU, as well as wireless protocols such as LoRaWAN network for data transmission to our cloud platform.
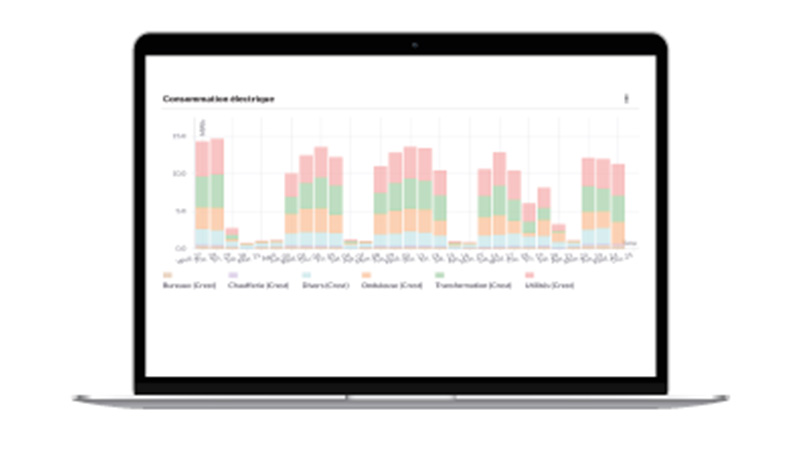
Energy management platform
The Power-Cloud platform allows you to visualize consumption and quality data at several scales, and to create energy efficiency analyses.
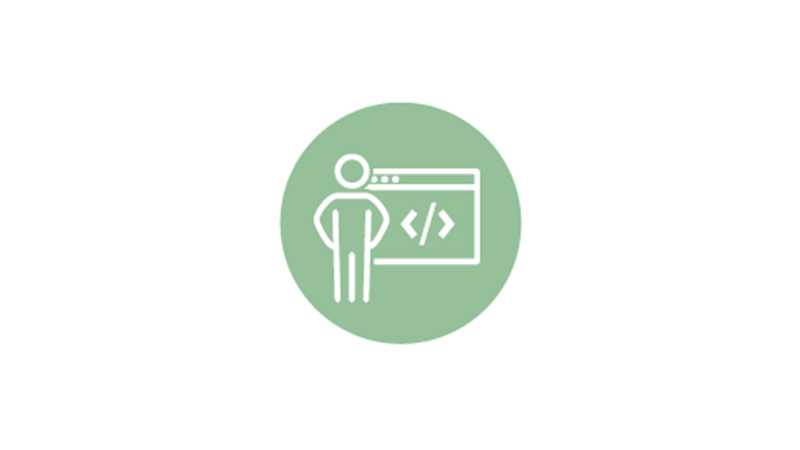
Who developed the solution?
The incomparably easy energy monitoring solution was developed by the French company Eco-ADAPT, which became 100% part of Schaeffler in March 2023.
What’s special
Power-Adapt is very easy to use and integrate. The initial costs are very low. With additional transmitters and sensors, the system can be used for much more than just energy measurement. For example, the pulse-transmitter can be used to convert conventional volume flowmeters (with pulse output) for gas, water, compressed air or steam into communicating measuring devices. Good to know: the solution may be eligible for country-specific government funding. In Germany, for example, the point of contact would be the Federal Office of Economics and Export Control (BAFA).