Table of contents
Yoke type ball bearing track rollers, stud type ball bearing track rollers
- Bearing design
- Load carrying capacity
- Compensation of angular misalignments
- Lubrication
- Sealing
- Speeds
- Noise
- Temperature range
- Cages
- Internal clearance
- Dimensions, tolerances
- Suffixes
- Structure of bearing designation
- Dimensioning
- Minimum load
- Design of bearing arrangements
- Mounting and dismounting
- Legal notice regarding data freshness
- Further information
Track rollers
Yoke type ball bearing track rollers, stud type ball bearing track rollers
Ball bearing track rollers:
- are ready-to-fit, single or double row rolling bearings based on deep groove or angular contact ball bearings ➤ Figure to ➤ Figure
- are supplied with or without a stud (designs without a stud are mounted on shafts or studs)
- have particularly thick-walled outer rings with a crowned or cylindrical outside surface ➤ section
- can support high radial loads ➤ section
- tolerate axial loads which are due to small misalignment defects, skewed running or temporary contact running impacts
- are sealed on both sides ➤ section
- are not mounted in a housing bore, but are supported on a flat mating track ➤ Figure and ➤ Figure
- can be adjusted to the mating track in the design with the eccentric collar, thus permitting, for example, larger manufacturing tolerances in the adjacent construction
Double row stud type track roller supported on a flat mating track
|
![]() |
Bearing design
Design variants
The bearings are available as:
- yoke type track rollers (single or double row) ➤ Figure
- stud type track rollers (single or double row) ➤ Figure to ➤ Figure
- track rollers with plastic outer tyre ➤ Figure
Ball bearing track rollers (general)
Characterised by a thick-walled outer ring
Ball bearing track rollers are self-retaining, single or double row ball bearings with particularly thick-walled outer rings. In addition to high radial forces, these bearings can also support axial forces in both directions. Ball bearing track rollers are available for various applications with an inner ring, with a stud and with a plastic tyre on the outer ring ➤ Figure to ➤ Figure.
Applications
Typical areas of application of these products include cam gears, bed ways, conveying equipment and linear guidance systems.
Outside surface profile of the outer ring
Spherical or cylindrical outside surface
Yoke type track rollers and stud type track rollers with a crowned outside surface have a radius of curvature of R = 500 mm. Yoke type track rollers with a cylindrical outside surface have the suffix X ➤ Table.
The crowned outside surface prevents edge stresses under skewing
Yoke type track rollers with a crowned outside surface are used where skewing can occur relative to the mating track. The crowned design reduces the risk of edge stresses ➤ link.
Corrosion protection by Corrotect
Special coating Corrotect
For applications requiring increased protection against corrosion, yoke type track rollers with the special Cr(VI)-free coating Corrotect are available by agreement as a special design; description of Corrotect ➤ link.
Yoke type track rollers
Comparable in design to deep groove or angular contact ball bearings
Yoke type track rollers are similar in construction to deep groove or angular contact ball bearings and are mounted on shafts or studs ➤ Figure. They have outer rings with a crowned or cylindrical outside surface, inner rings and ball and cage assemblies with plastic cages. Yoke type track rollers LR6, LR60 and LR2 are single row, LR50, LR52 and LR53 are double row.
Double row design
LR52, LR53
While the outer dimensions remain unchanged, the internal construction of yoke type track rollers LR52 and LR53 has been optimised. This has brought about an increase in load carrying capacity and speed in continuous operation, and in grease lubrication nD G. These yoke type track rollers are X-life bearings ➤ link.
Yoke type track rollers, sealed on both sides Fr = radial load Fa = axial load
|
![]() |
Stud type track rollers
Heavy-section roller stud, with or without eccentric collar
Stud type track rollers have outer rings with a crowned outside surface, heavy-section roller studs and ball and cage assemblies with plastic cages ➤ Figure and ➤ Figure. The yoke type track rollers are available with and without an eccentric collar.
For ease of mounting, the roller stud is produced in one of the following designs:
- with a threaded hole and mounting slot ➤ Figure
- with an external thread and hexagonal socket ➤ Figure
- with an external thread and flat areas on both sides ➤ Figure.
Track rollers ZL2 are single row, ZL52, ZLE52 and KR52 are double row.
Design without eccentric collar
Stud type track rollers without an eccentric collar are suitable for applications where a defined requirement for adjustment in relation to the mating track on the adjacent construction is not required ➤ Figure and ➤ Figure.
Stud type track rollers, without eccentric collar, short roller stud with threaded hole, sealed on both sides Fr = radial load Fa = axial load
|
![]() |
Stud type track roller, without eccentric collar, long roller stud with external thread, sealed on both sides Fr = radial load Fa = axial load
|
![]() |
Design with eccentric collar
Stud type track rollers ZLE52 have an eccentric collar ➤ Figure. The eccentric collar can be used to set the outside surface of the outer ring clearance-free against the mating track. This gives optimum geometrical locking between the track roller and mating track. Furthermore, larger manufacturing tolerances can be tolerated in the adjacent construction. The load distribution when several stud type track rollers are used is also more uniform. For countertensioning during fitting, this series has flat areas on both sides of the roller stud. Threaded connections must be provided on the two end faces for relubrication, dimensions ➤ link.
Stud type track roller, with eccentric collar, long roller stud with external thread, sealed on both sides Fr = radial load Fa = axial load
|
![]() |
Track rollers with plastic outer tyre
Suitable for low loads and high demands on low-noise running
Track rollers KLRU and KLRZ comprise single row deep groove ball bearings with a shrink-fitted polyamide outer ring (PA) ➤ Figure. Polyamide can tolerate higher specific contact pressures than elastomer and is relatively resistant to abrasion. These track rollers are mounted on shafts or studs and are used where low loads are present and the bearings are required to run particularly quietly.
Outside surface profile of the outer ring
Spherical or cylindrical outside surface
Track rollers KLRU have an outer ring with a crowned outside surface. The radius of curvature is indicated in the product table. Series KLRZ has a cylindrical outside surface.
Maximum radial load
The maximum radial load is determined by the permissible contact pressure; the values Fr per in the product tables must not be exceeded.
Track rollers with plastic outer tyre, sealed on both sides Fr = radial load Fa = axial load
|
![]() |
X-life premium quality
Track rollers LR52 and LR53, which have undergone comprehensive further development, are supplied in the X-life design. These track rollers are characterised by a longer rating life and operating life, due to higher basic dynamic load ratings compared with standard track rollers.
This higher performance results from the use of state of the art manufacturing techniques and improved internal constructions. They lead to better and more uniform surfaces and contact areas and thus optimised load distribution in the bearing.
Increased customer benefits due to X-life
This opens up expanded design possibilities:
- Under the same load and with an unchanged design envelope, X-life bearings have a longer rating life. Maintenance intervals can be extended
- Conversely, an X-life bearing in the same design envelope and with the same rating life can support higher loads
- Where the rating life and load remain unchanged, X-life bearings allow higher performance density, facilitating optimisation of the design envelope and reductions in mass
Lower operating costs, higher machine availability
In conclusion, these advantages improve the overall cost-efficiency of the bearing position significantly and thus bring about a sustainable increase in the efficiency of the machine and equipment.
Suffix XL
X-life track rollers include the suffix XL in the designation.
Load carrying capacity
Suitable for high radial loads
The track rollers can support high radial loads as well as axial loads arising from slight misalignment and skewed running.
Installation as track roller
If used as a track roller, the outer ring undergoes elastic deformation
In the case of track rollers, the outer ring is supported on the mating track at certain points and undergoes elastic deformation (oval deformation) ➤ Figure. Compared to rolling bearings supported in a housing bore, track rollers therefore have:
- a modified load distribution in the bearing (load is supported by fewer rolling elements in the loaded zone). This is taken into consideration by the reduced effective basic load ratings Cr w and C0r w used in the calculation of the rating life
- bending stresses and reverse bending strengths in the outer ring. These are taken into consideration by the permissible effective radial loads Fr per and F0r per. The bending stresses and reverse bending strengths must not exceed the permissible strength values of the material
Installation as track roller: deformation of the outer ring when used against a flat mating track |
![]() |
Compensation of angular misalignments
Not suitable for the compensation of angular misalignments
Track rollers are not suitable for the compensation of angular misalignments, but can tolerate small misalignments and slight skewed running; for limits see chapter Yoke type track rollers, stud type track rollers ➤ link.
Skewed running
Misalignment leads to additional axial loading of the bearing and to elastic axial slippage in rolling contact between the outer ring and the raceway.
Tilted running
If tilting occurs during running, increased edge stresses occur, especially in track rollers with a cylindrical outside surface of the outer ring. Track rollers with a crowned outer ring are less sensitive to tilting and should therefore be used in preference if tilting is expected.
Lubrication
Greased using a grease to GA13
The track rollers are greased using a lithium soap grease to GA13. In the case of stud type track rollers, series ZLE52 can be relubricated via the roller stud. Track rollers with a plastic outer tyre cannot be relubricated. Suitable greases for relubrication ➤ Table.
LR52, LR53
Double row track rollers are also greased using a lithium soap grease to GA13. Due to the improved internal construction, less friction occurs and less strain is placed on the lubricant. This leads to lower bearing temperatures.
Two contact zones
Lubricate the rolling elements and mating track
Two contact zones must be lubricated and considered separately:
- the rolling elements and rolling element raceway
- the outside surface of the track roller and the mating track
Track rollers are also available as a special design with a lubrication hole in the inner ring. These bearings have the suffix IS1 ➤ Table.
Sealing
Yoke type track rollers
Bearings with the suffix 2RSR
Yoke type track rollers with the suffix 2RSR have lip seals with radial sealing action on both sides. In some sizes, RS seals with axial sealing action are fitted for reasons of space.
2HRS or 2Z seal
Double row yoke track rollers in X-life quality have a revised sealing concept with a significantly improved sealing action compared to the previous design ➤ Figure. Further information on HRS seals ➤ Table. As standard, the bearings (suffix 2HRS) have DEHP-free lip seals on both sides.
Lip seal 2HRS or sealing shield 2Z
|
![]() |
Stud type track rollers
Series ZL2 and ZL52
Stud type track rollers ZL2 and ZL52 have lip seals on the stud side and the suffix DRS. The opposite side can be sealed using the plastic cover supplied.
Series ZLE52
Stud type track rollers ZLE52 have sealing shields on both sides and the suffix 2Z.
Track rollers with plastic outer tyre
Sealing shields or lip seals
These track rollers have sealing shields on both sides (suffix 2Z) or lip seals with radial sealing action (suffix 2RSR).
Speeds
Speeds nD G
The maximum permissible speed for track rollers is essentially determined by the permissible operating temperature of the track rollers. The temperature thus depends on the type of bearing, the load, the lubrication conditions and the cooling conditions.
Speeds with lip seals
The speed of track rollers with lip seals is additionally restricted by the permissible sliding speed at the seal lip.
Speeds during continuous operation
The speeds nD G in the product tables are guide values and are valid for grease lubrication.
Additional information on the subject of speeds in the chapter Yoke type roller bearing track rollers, stud type roller bearing track rollers must be observed ➤ section.
Noise
Schaeffler Noise Index
The Schaeffler Noise Index (SGI) is not yet available for this bearing type ➤ link. The data for these bearing series will be introduced and updated in stages.
Temperature range
Limiting values
The operating temperature of the track rollers is limited by:
- the dimensional stability of the bearing rings and rolling elements
- the cage
- the lubricant
- the seals
- the plastic outer tyre
Possible operating temperatures of the track rollers ➤ Table.
Permissible temperature ranges
Operating temperature |
Yoke type track rollers |
|
---|---|---|
with plastic outer tyre KLRU and KLRZ |
without plastic outer tyre |
|
|
–20 °C to +80 °C |
–20 °C to +120 °C |
In the event of anticipated temperatures which lie outside the stated values, please contact Schaeffler.
Cages
Solid cages made from polyamide PA66 are used as standard
The cages used in the track rollers are plastic cages made from glass fibre reinforced polyamide PA66. These cages have a low mass as well as good sliding and emergency running characteristics. Track rollers in the X-life design have an optimised polyamide cage as standard.
Internal clearance
Radial internal clearance
The standard is CN
Track rollers are manufactured as standard with radial internal clearance CN (normal) ➤ Table. CN is not stated in the designation.
The values for radial internal clearance correspond to DIN 620-4:2004 (ISO 5753-1:2009). These are valid for bearings which are free from load and measurement forces (without elastic deformation).
Radial internal clearance for yoke and stud type track rollers
Nominal |
Radial internal clearance |
||||||||||
---|---|---|---|---|---|---|---|---|---|---|---|
d |
C2 |
CN |
C3 |
C4 |
C5 |
||||||
mm |
μm |
μm |
μm |
μm |
μm |
||||||
over |
incl. |
min. |
max. |
min. |
max. |
min. |
max. |
min. |
max. |
min. |
max. |
2,5 |
10 |
0 |
7 |
2 |
13 |
8 |
23 |
14 |
29 |
20 |
37 |
10 |
18 |
0 |
9 |
3 |
18 |
11 |
25 |
18 |
33 |
25 |
45 |
18 |
24 |
0 |
10 |
5 |
20 |
13 |
28 |
20 |
36 |
28 |
48 |
24 |
30 |
1 |
11 |
5 |
20 |
13 |
28 |
23 |
41 |
30 |
53 |
30 |
40 |
1 |
11 |
6 |
20 |
15 |
33 |
28 |
46 |
40 |
64 |
40 |
50 |
1 |
11 |
6 |
23 |
18 |
36 |
30 |
51 |
45 |
73 |
50 |
65 |
1 |
15 |
8 |
28 |
23 |
43 |
38 |
61 |
55 |
90 |
Dimensions, tolerances
The dimensions of special bearings (F../Z..) may deviate from the standard.
Tolerances
The tolerances for the dimensional and running accuracy of track rollers correspond to tolerance class Normal in accordance with ISO 492:2014. In a deviation from ISO 492, the diameter tolerance of the profiled outside surface is 0/–0,05 mm.
Stud tolerances
The stud diameter tolerances for stud type track rollers are:
- in tolerance class r6 for ZL2 and ZL52
- in tolerance class h7 for KR52
- in tolerance class h9 for ZLE52
Suffixes
For a description of the suffixes used in this chapter ➤ Table and medias interchange http://www.schaeffler.de/std/1B69.
Suffixes and corresponding descriptions
Suffix |
Description of suffix |
|
---|---|---|
DRS |
Lip seal on stud side, axial sealing action |
Standard |
IS1 |
Lubrication hole in inner ring |
Special design, available by agreement |
RR |
Protected against corrosion by Corrotect special coating |
Special design, available by agreement |
TVH |
Cage made from glass fibre reinforced polyamide |
Standard |
X |
Cylindrical outside surface |
Standard |
XL |
X-life design |
Standard |
2HRS |
Lip seal on both sides with optimised geometry, low friction |
Standard |
2RS |
Lip seal on both sides, with axial sealing action |
Standard |
2RSR |
Lip seal on both sides, with radial sealing action |
Standard |
2Z |
Sealing shield on both sides |
Standard |
Structure of bearing designation
Examples of composition of bearing designation
The designation of bearings follows a set model. Examples ➤ Figure to ➤ Figure.
Single row yoke type track roller, lip seal on both sides: designation structure |
![]() |
Double row yoke type track roller, 2HRS seal on both sides, cage made from glass fibre reinforced polyamide, X-life design: designation structure |
![]() |
Double row stud type track roller with eccentric collar, sealing shield on both sides: designation structure |
![]() |
Dimensioning
Calculation of the rating life
The methods for calculating the rating life are:
- the basic rating life to DIN ISO 281
- the adjusted basic rating life to DIN ISO 281
- the expanded calculation of the adjusted reference rating life to DIN ISO 281-4
Use effective basic dynamic/ static load ratings
These methods are described in the chapter Load carrying capacity and life. For track rollers, the following values must be replaced:
- Cr, C0r = Cr w, C0r w
Effective basic dynamic or static load rating - Cur = Cur w
Fatigue limit load as track roller
Further equations for calculating the rating life and given in the chapter Yoke type track rollers, stud type track rollers. The instructions and information provided there must be observed.
Static load safety factor
S0 = C0r w/F0r
In addition to the basic rating life L, it is also always necessary to check the static load safety factor S0 ➤ Equation.
Static load safety factor
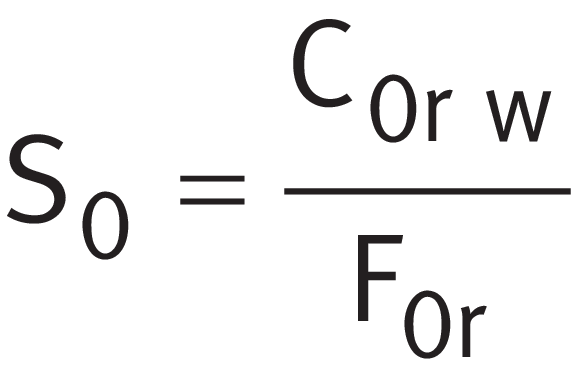
Legend
S0 | - |
Static load safety factor |
C0r w | N |
Effective radial basic static load rating in accordance with product table |
F0r | N |
Maximum static radial load on track roller |
Track rollers are regarded as heavily loaded at a static load safety factor of S0 < 8. Static load safety factors of S0 < 1 cause plastic deformation of the rolling elements and the raceways, which can impair smooth running. This is only permissible for bearings with small rotary motions or in secondary applications.
If an application has a static load safety factor S0 < 2, please consult Schaeffler.
Minimum load
Minimum load C0r w/Fr < 60
In order to ensure that the outer ring is driven, that no slippage occurs and that the track roller does not lift from the mating track, the track roller must be subjected to a minimum load in dynamic operation. In general, the minimum load is calculated using the ratio C0r w/Fr < 60.
Design of bearing arrangements
Adjacent construction of track rollers
The value for dimension “d2” must not be less than the value stated
The abutment surfaces for the bearings must be flat and perpendicular. Due to the contact pressure occurring, they must not be less than the dimension d2; see product tables for values ➤ link.
Yoke type track rollers LR
Yoke type track rollers LR can be axially clamped or located by means of conventional fasteners such as snap rings.
Shaft tolerances
Tolerance class h6 Ⓔ
In general, yoke type track rollers have point load on the inner ring. In order to ensure adequate support and to largely avoid fretting corrosion, the shaft tolerance should be in the tolerance class h6 Ⓔ.
Adjacent construction of stud type track rollers
The value for dimension “d2” must not be less than the value stated
The abutment surfaces for the track rollers must be flat and perpendicular. Due to the contact pressure occurring, they must not be less than the dimension d2; see product tables for values ➤ link.
Lead chamfer
The lead chamfer on the locating bore must not be more than 0,5×45°.
Stud type track rollers ZL and KR must be axially clamped. The abutment surface for the nut must have sufficiently high strength and the tightening torque MA for the fixing nut must be observed; see product table for values ➤ link. The roller stud can only transmit the permissible radial load if the correct tightening torque is applied. If the tightening torque cannot be adhered to, an interference fit is required.
Locating bore tolerance
Tolerance class H7 Ⓔ
For series ZL2, ZL52, KR52 and ZLE52, Schaeffler recommends locating bores to tolerance class H7 Ⓔ.
Mounting and dismounting
The mounting and dismounting options for track rollers, by mechanical or hydraulic methods, must be taken into consideration in the design of the bearing position.
Schaeffler Mounting Handbook
Rolling bearings must be handled with great care
Rolling bearings are well-proven precision machine elements for the design of economical and reliable bearing arrangements, which offer high operational security. In order that these products can function correctly and achieve the envisaged operating life without detrimental effect, they must be handled with care.
The Schaeffler Mounting Handbook MH 1 gives comprehensive information about the correct storage, mounting, dismounting and maintenance of rotary rolling bearings http://www.schaeffler.de/std/1B68. It also provides information which should be observed by the designer, in relation to the mounting, dismounting and maintenance of bearings, in the original design of the bearing position. This book is available from Schaeffler on request.
Mounting guidelines for yoke type track rollers
Guidelines
If the tolerances are unfavourable, the yoke type track rollers should be pressed onto the shaft or stud using a mounting press ➤ Figure. The inner ring must be fitted such that the pressing-in force is distributed uniformly on the end face of the inner ring. The press-in force must not be directed through the rolling elements. Ensure that the seals are not damaged while mounting the yoke type track rollers. Yoke type track rollers must be secured axially after mounting.
Mounting of yoke type track roller using a mounting press
|
![]() |
Stud type track rollers
Guidelines for mounting
Stud type track rollers are mounted and dismounted using the methods applied to yoke type track rollers ➤ Figure. The tightening torques MA given in the product tables must be observed. It is only in this way that the permissible radial load can be ensured. Screws and nuts of grade 8.8 or better must be used.
Mounting of stud type track roller |
![]() |
Legal notice regarding data freshness
The further development of products may also result in technical changes to catalogue products
Of central interest to Schaeffler is the further development and optimisation of its products and the satisfaction of its customers. In order that you, as the customer, can keep yourself optimally informed about the progress that is being made here and with regard to the current technical status of the products, we publish any product changes which differ from the printed version in our electronic product catalogue.
We therefore reserve the right to make changes to the data and illustrations in this catalogue. This catalogue reflects the status at the time of printing. More recent publications released by us (as printed or digital media) will automatically precede this catalogue if they involve the same subject. Therefore, please always use our electronic product catalogue to check whether more up-to-date information or modification notices exist for your desired product.
Further information
For reliable and problem-free operation of track rollers, it is essential that attention is paid to the following information in the chapter Yoke type track rollers, stud type track rollers: